|
Post by whalecottagedesigns on Oct 27, 2024 0:56:18 GMT -5
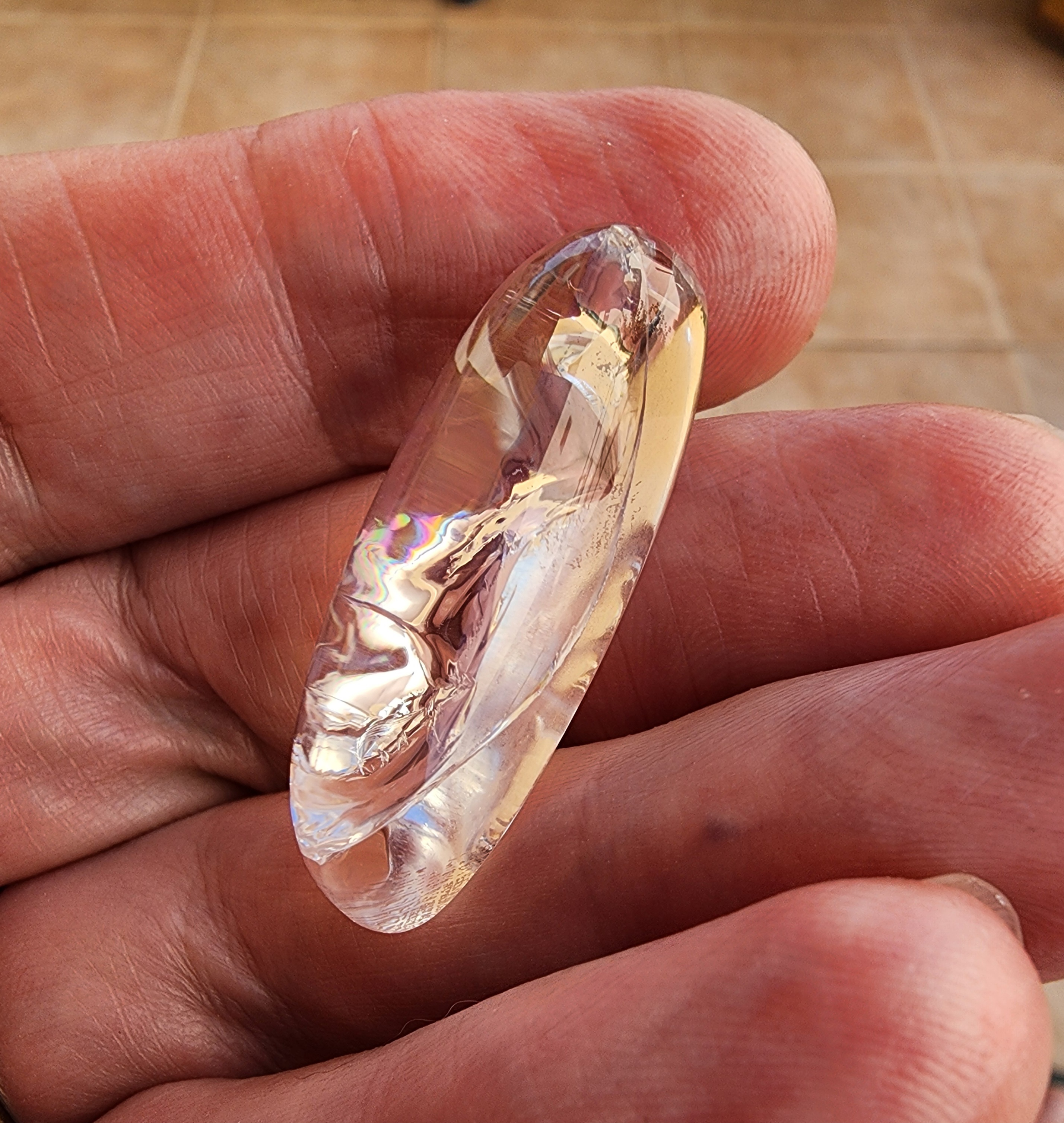 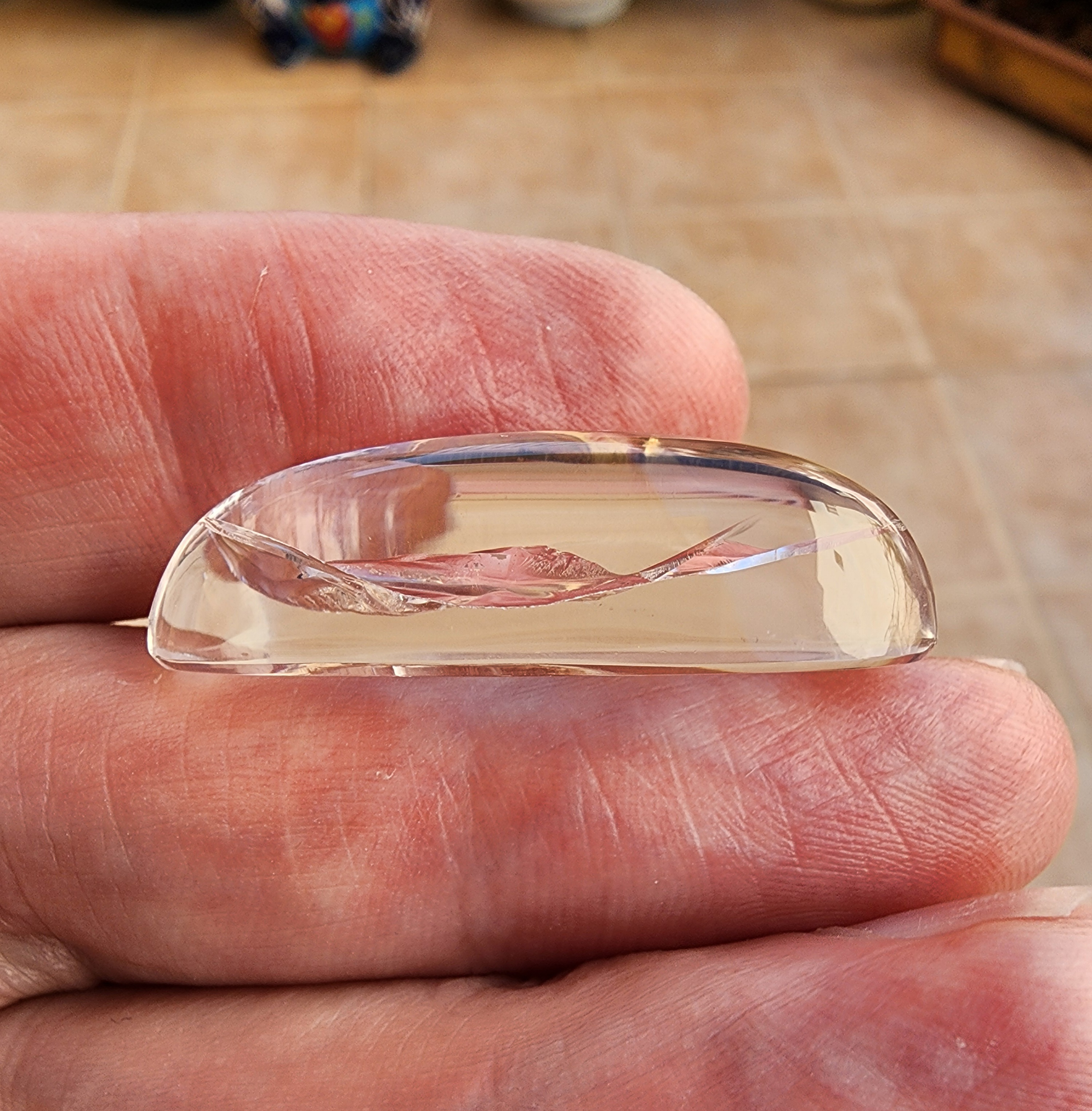 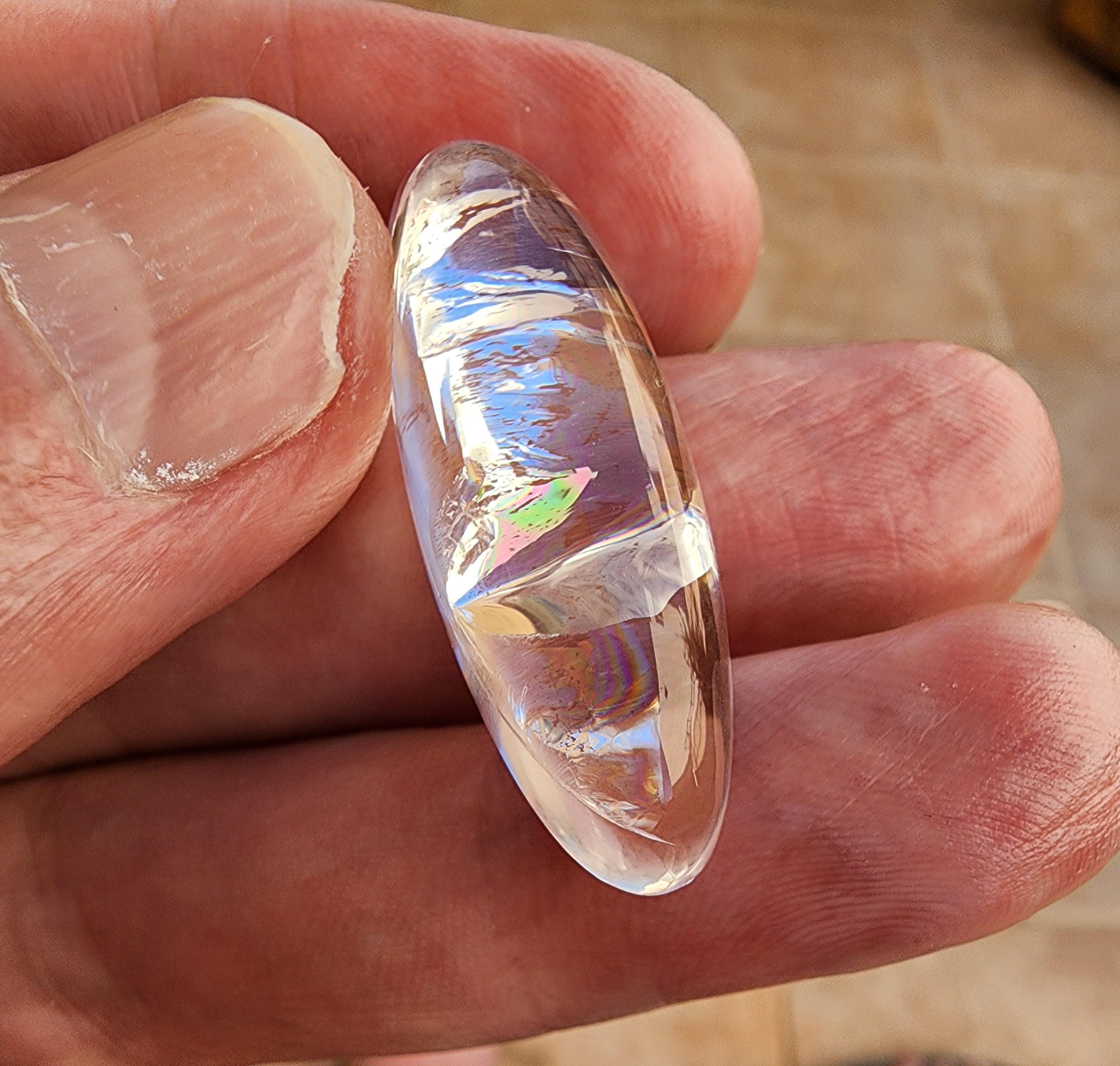 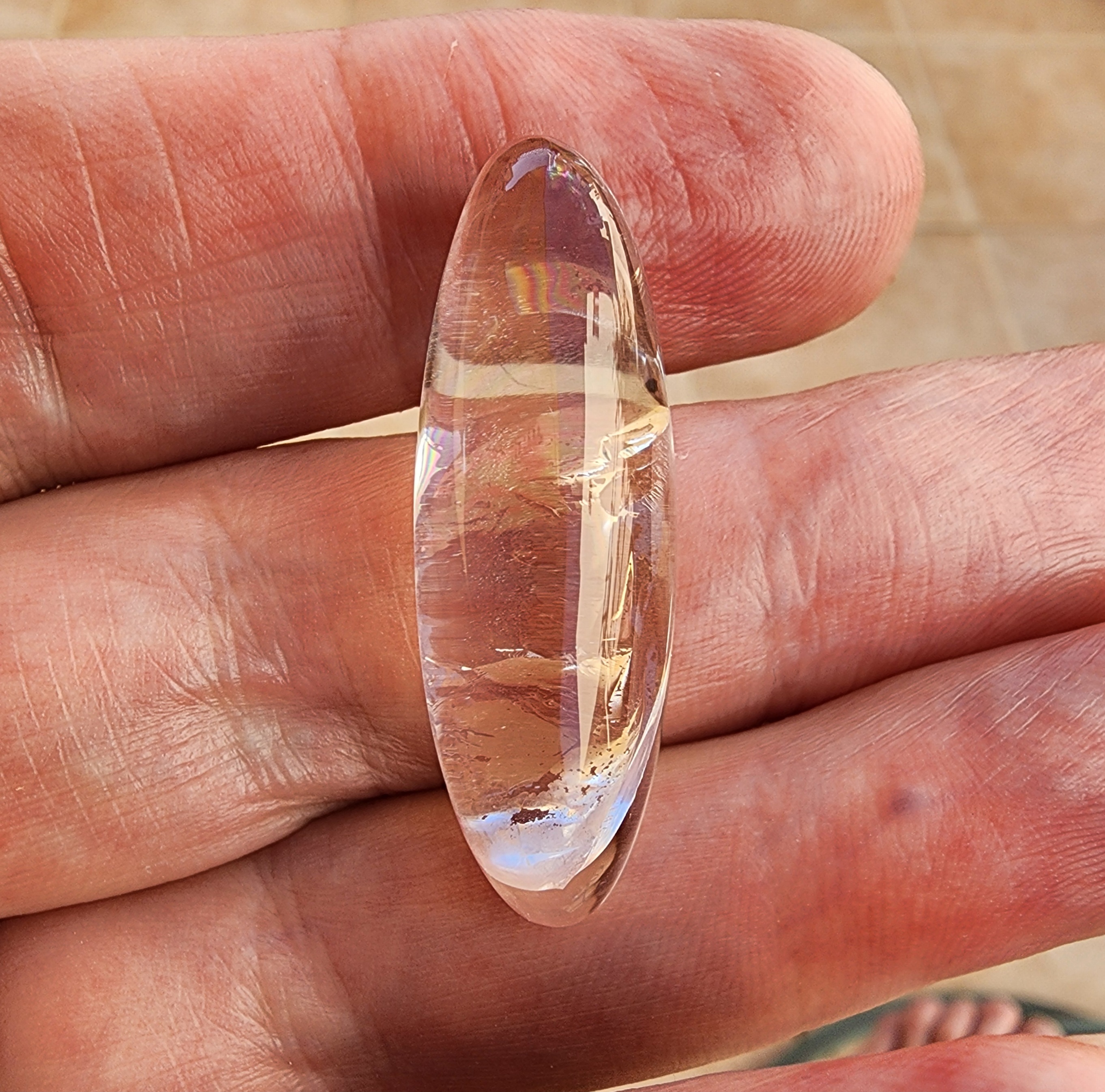 Thought I would start a new thread here, based on a question from realrockhound about my final polish after the 3K wheel. This is about as good as I can get a quartz cab with my present two and a half year experience and method for final polish. Maybe other folk can jump in and give ideas and pointers on their own final polishes too! I will just copy and paste my answer to him on the previous Turkish Chrome Chalcedony thread below here! For all of my quartzes including the micro- and cryptocrystalline versions I go straight from 3K to Linde-A (100K equivalent) on leather. Like Zam for Malachite, or dry T-shirt material for Amber, this really is the silver bullet polish for quartzes for me! I use a water spray bottle with roughly 6 teaspoons in about half a litre of water, just for the record. And sometimes with a really beautiful cab, before I start, I will sprinkle a little "extra", maybe a quarter of a teaspoon on the previously pre-wetted (sprayed with the solution) leather wheel before I spin it on the side on the Cabking. I spray the leather with the solution when I hit the 1200 wheel so that the leather soaks up the moisture by the time I am done with the 3000 grit. I will polish the cab until it starts to "tug", starts to dry, then spritz with the water bottle solution. I hope this makes sense! And as I am still learning, this is still quite the enigma wrapped in a puzzle to me, as up to the 3K, one has to roughly double the grits. 80 to 220 to 280 to 600 etc... But the jump straight from 3K to 100K works incredibly well on quartz. And I really do not have to spend much time on final polish either, it goes seriously quickly there, maybe a minute or two! Compared with 5 minutes or more spent on each of the other wheels.
|
|
|
Post by whalecottagedesigns on Oct 27, 2024 1:01:29 GMT -5
And as you can see from my thumb nail, apart from very small cabs, I use my hands to cab, not dops.. :-)
Also, my little 5 inch leather wheel that spins on the right hand side of the Cabking, is slowly getting to its end of life, and the guys who I bought it from (I forget now, but think it was Diamond Pacific) are not making and selling them anymore. So I have made up my own 8 inch leather one using 3M double sided tape to stick a piece of thickish leather on an acrylic backing plate for use on the 8 inch slanted cabber. Have not used it yet as the small one is still working fine. The two advantages I see there are that one can regulate the speed on the slanted cabber, which may be useful, and also it is a much bigger leather surface to work on, so I have high hopes for it!
|
|
realrockhound
Cave Dweller
Chucking leaverite at tweekers
Member since June 2020
Posts: 4,483
|
Post by realrockhound on Oct 27, 2024 9:58:32 GMT -5
I think I just need to get some new polishing compounds. I’m getting a good polish on my stones but something is just lacking. I’m beginning to think the stuff I have I just old or bad. Think I’m going to get some different types of pads and a few different polishing compounds. I’m thinking at this point it’s not me, and just what I have.
|
|
|
Post by liveoak on Oct 27, 2024 10:55:06 GMT -5
Well, you sure proved that !! Guess I should give it a try. Thanks for sharing the tip, Patty
|
|
|
Post by chris1956 on Oct 27, 2024 12:23:54 GMT -5
I have never been a fan of polishing compounds but after your last two examples I am going to have to try it. What type of leather did you use on the pad you made? Thanks for sharing this!
|
|
|
Post by whalecottagedesigns on Oct 27, 2024 19:17:32 GMT -5
realrockhound I would bet it is your compound that may be old, because for sure I do not have that much practice so it is not a technique thing. I know that lapidary1234 had mentioned another brand AO (Aluminium Oxide) polish that was much less expensive than the Linde-A. And it was from a company in the US somewhere, but I forget what it was called. Hopefully he reads this thread and will add it in here! liveoak Thank you Patty, and very much my pleasure! chris1956 My pleasure Chris! I just bought a big section of thickish (maybe 2mm) brown cow leather off Amazon. Note that I have not used that one yet, it has been made up and is waiting for when my small Cabking one dies on me. For interest's sake, if you were not using polishing compounds what were you yourself using for final? The diamond paste? If so, I stopped using it because it was quite dear, and as I cab using my hands, it was just too slippery for me! :-) Another reason we stopped using it was that Naykie (my wife Sheugnet) was getting into cutting Ethiopian Opal, and we did not want that heavily hydrophane material soaking up the waxy binder.
|
|
|
Post by whalecottagedesigns on Oct 27, 2024 19:22:06 GMT -5
And a general note here, while I am very happy with Linde-A on leather for the quartzes, and Zam for softies like Malachite and Turquoise, and the dry cotton T-shirt material for Amber, I am still struggling badly with undercutting rocks. Any of the multi-mineral rocks that undercut still beat me into the ground! :-)
|
|
|
Post by chris1956 on Oct 27, 2024 19:49:28 GMT -5
realrockhound I would bet it is your compound that may be old, because for sure I do not have that much practice so it is not a technique thing. I know that lapidary1234 had mentioned another brand AO (Aluminium Oxide) polish that was much less expensive than the Linde-A. And it was from a company in the US somewhere, but I forget what it was called. Hopefully he reads this thread and will add it in here! liveoak Thank you Patty, and very much my pleasure! chris1956 My pleasure Chris! I just bought a big section of thickish (maybe 2mm) brown cow leather off Amazon. Note that I have not used that one yet, it has been made up and is waiting for when my small Cabking one dies on me. For interest's sake, if you were not using polishing compounds what were you yourself using for final? The diamond paste? If so, I stopped using it because it was quite dear, and as I cab using my hands, it was just too slippery for me! :-) Another reason we stopped using it was that Naykie (my wife Sheugnet) was getting into cutting Ethiopian Opal, and we did not want that heavily hydrophane material soaking up the waxy binder. I polished a lot of Petoskey stones and most of them have very small holes. Any sort of polish or paste would get stuck in those holes and is very difficult to get out (although I haven't tried to with the ultrasonic cleaner and textile cleaner than I now have. I purchased 14K and 50K grit wheels for my cabber. This seems to do real well on most stones but I have to say I don't think I have gotten a polish as good as the last two examples you gave.
|
|
lapidary1234
spending too much on rocks

"If you like rocks you can't be all bad!!" ~ old timer quote
Member since October 2021
Posts: 293
|
Post by lapidary1234 on Oct 27, 2024 20:10:23 GMT -5
Not sure who to tag here but the submicron polish i found is called rapid polish #61. MN lapidary supply owns the patents for it and manufactured it in MN so that is the cheapest place to buy it. You have to call, I don't think they have online ordering. On the other hand, if you call in the morning there is a good chance you can speak to the owner directly. His name is Val and has lots of good advice/perspective.
On the notion of doubling the grit number as you progress, I've wondered about this as well. I have my thoughts that it is because the scratches left after a 3,000 grit wheel are small enough that going to an oxide compound can actually buff them out. That said, if you take a magnifying glass (or loupe) and get a reflection on the surface of the stone, I typically can still see scratches after 3,000. Sometimes I obsess and start examining the reflection even further and I usually can still see scratches after even an 8,000 and 14,000 grit wheels.
This is where I believe the folks who mention the "electro-chemical" reaction that an oxide polish gives are correct. An old timer explained it as kind of melting the surface...giving the stone an entirely new finish.
Fwiw, the only stones I've ever looked at with a reflection on extreme magnification that don't show some microscopic scratches have either been tumbled or possibly vibe lapped. I have been trying real hard not to obsess over perfection though as id like this to remain a hobby I enjoy. If you find one of these it will almost blind you from the mirror like reflection!
|
|
|
Post by whalecottagedesigns on Oct 27, 2024 21:10:02 GMT -5
chris1956 That makes sense about the Petoskey stones! lapidary1234 Thank you for the information! And I agree, I also do not want to go down the 200K rabbit hole of polishing, if it is shiny to my eye, that is good enough for me.
|
|
|
Post by whalecottagedesigns on Oct 27, 2024 22:49:38 GMT -5
lapidary1234 And your mention of the "electo chemical" polishing reaction takes me to something else we can pursue! The video that got me interested in this is the one called "Best Polishing Powder For Opal And Gemstones? Chemical Mechanical Polishing Metal Oxides vs Diamonds" by Roys Rocks on YouTube. He is a proper scientist by day, but an Australian opal carver by night (polishes and carves using a Dremel type machine). The video is a really interesting watch! A quickie summation I got from it is that the very hard diamond works purely in a mechanical fashion. Same way that all the other diamonds on your wheels do, by producing super fine scratches that are just not visible to the eye. No chemical action. Then Aluminium Oxide (Linde-A etc) works by mostly mechanical, but also a smaller chemical polishing part. Then Cerium Oxide works on a mostly Chemical way, but with a bit of mechanical action thrown in. Possibly due to the fact that Cerium Oxide is roughly on average a Mohs 6, while diamond is well, you know, and Aluminium Oxide is also very hard at a Mohs 9. His arguments are based on his own experience and he also points at a scientific paper that I would love to get ahold of without having to pay a bunch of money as I am not in academia anymore for quite some time now. Anyone still able to get these for free, please share if you can!. It is "PERFORMANCE CHARACTERIZATION OF CERIUM OXIDE ABRASIVES FOR CHEMICAL-MECHANICAL POLISHING OF GLASS by Robert Sabia & Harrie J. Stevens" Now the chemical polishing he talks about is called "Chemical Mechanical Planarization". The Planarization bit just means polishing really. So it is chemical mechanical polishing or PMP. I assume this is the same thing as the "electro chemical" that lapidary1234 was talking about. And a way to think of it is as a much less aggressive type of acid etching. Some of how he explains it goes above my head, which is why I would like to read that paper. But what I get is that using Cerium Oxide, along with water, bonds to the surface of the stone and then takes "a little bit away". That bit I don't understand :-) The bit that confuses me is that Roy says this PMP with Cerium needs a fair bit of water to work properly. But the old-timey books like guru Sinkankas says that the polishing works the best at the point where your polishing slurry starts to dry (obviously you cannot let it dry out fully as heat etc could damage your surface). But he says that when the stone starts to "tug" that is where the very best polishing takes place. And I have read some folks say that you at that point "melt" the surface of a stone into a mirror polish. These seem like opposing views!
|
|