pizzano
Cave Dweller
Member since February 2018
Posts: 1,390
|
Post by pizzano on May 6, 2020 13:24:05 GMT -5
I should have stated.......A new receipt to me....!
I've been using Covington's Tumbler Polish (98% pure Alumina) as a pre and Gold Polish #2 (99% pure micro Alumina) or Cerium Oxide as the polish compounds, after 500 SC/AO stages, in the Vibe with various size ceramics, for over 3yrs now. 99% of the time, regardless of stone type, my results have been very good to excellent hobby grade finishes........especially, due to hand grind and preform prior, on diamond faceting disc's.
Since, my go to media supply buddies (Covington Engineering) moved to Idaho, and no longer down the street from one of my clients, On-Line shopping with them is my only recourse.........and of course, their retail and shipping prices have gone up, almost 40%. Now, they were never a cheap alternative, but very knowledgeable and extremely helpful. Their media products were (are) top notch and increased my tumbling successes 10 fold.......!
So, I've decided to give The Rock Shed a little more of my business. Spent plenty there purchasing rough material, but never any compounds or ceramic media.......since I ran out of pre-polish and polishing media, I just received my package from them (always great shipping turn-a-round times), and now have plenty of AO 1000, AO Polish compounds along with fresh ceramic media.
I'm about to start the pre-polish (AO 1000) and final polishing of a batch that was started back in March.....:
Everything has been through vibe SC 120/220 & AO 500 and looking ready to go........and since many of you Rock Shed fans have been pleased with your results after using their media & compounds, just wondering if there are any things I should be aware of (surprises or unexpected pleasures) now that I'm trying a "new" receipt......!
|
|
Wooferhound
Cave Dweller
Lortone QT66 and 3A
Member since December 2016
Posts: 1,432
|
Post by Wooferhound on May 8, 2020 6:27:51 GMT -5
Do you have a receipt for your recipe ?
|
|
Fossilman
Cave Dweller
Member since January 2009
Posts: 20,723
|
Post by Fossilman on May 8, 2020 9:48:12 GMT -5
Always satisficed with the grit media from the rock shed....
|
|
pizzano
Cave Dweller
Member since February 2018
Posts: 1,390
|
Post by pizzano on May 8, 2020 11:11:42 GMT -5
Do you have a receipt for your recipe ? LOL.......yes.
In this particular case, the stones being vibe tumbled are a mix of self collected quartz, agate, all in the 6-7 Mohs range........none of which are without some kind of internal softer properties, noticed this while cutting and preforming. So, I expected some fractures, pitting and surface undulations.
Nothing out of the ordinary with the beginning grind process.....:
Raytech TV-5 bowl on a Lyman Turbo vibe......this bowl full weighs around 4lbs. I normally come in around 5lbs for most tumbles.
1st Vibe stage - 1.5 tbl spoons of SC 120/220 and 2/3rds the stone volume of various older used ceramics......it a small batch of stones. Tumbled 24hrs.
2nd Vibe stage - 1.5 tbl spoons of AO 500. Same ceramic's and volume. Tumbled 24hrs..........this is when the stone imperfections exposed themselves.
Now for pre-polish and polishing stages.......:
3rd Vibe stage - 1.25 tbl spoons of Rock Shed's AO 1000 and 2/3rds the rock volume of Rock Shed's "small" ceramics (new). Tumbled 12hrs, not happy....! cleaned and recharged tumbled another 12hrs. Better results, but by this time (18hrs) I would have had a nice shine (not deep), with same type of stone material I've polished before, using Covington's "Tumbler Polish" as the pre-polish. The "new" ceramics worked as expected. The Rock Shed 1000 is a little more difficult than Covington's to remove while cleaning. I used my standard method of 2hr run with dish soap added to bowl prior to clean-out and then Borax stone scrub.
4th Vibe stage - 1tbl spoon of Rock Shed's AO Polish......needed to add another 1/2tbl spoon about 4hrs into the run to get proper slurry. Same ceramics and volume, tumbled 12hrs, not happy.....!....Shine was not deep enough and again the clean-up (same as previous) was more difficult. So, I ran the stones through another 12hr cycle same as previous, now at 24hrs total. Using Covington's Gold Polish #2 or Cerium Oxide, all things equal, I would have gotten a very deep shine after 18hrs and clean-up would have been less painstaking.
Now, after the 24hr, 4th vibe stage AO Polish......it didn't get any better or leave the deep shine I expected, I'm into a 3rd polishing stage (5th overall). So, I'm currently using a trick I've tried before with this type of stone material when I didn't have Covington's compounds...It worked, but took time to get a deep shine (another 12hrs).......:
5th Vibe stage - 1tbl spoon of Cerium Oxide, 2/3rd's the stone volume of older ceramics specifically used for Cerium Oxide polishing. I'll check it every 3hrs (currently into the first hour), and see what I get.......Like a I stated previously, the stone quality to begin with, was not that great. So there will be imperfections.........But I want at least a deep glossy shine, which I've come to expect (in the past) from this material..........  ..........LOL
|
|
jamesp
Cave Dweller
Member since October 2012
Posts: 36,612
|
Post by jamesp on May 9, 2020 5:24:26 GMT -5
The allowable aluminum oxide particle size variation for a given grit size is laughable pizzano. If we think we are buying pure AO 500 sized particles when we buy AO 500 we are sadly mistaken. Abrasive companies are allowed to market abrasives with huge variations in size. This allowance is totally deceptive to the unknowing consumer. For example Kramer sells a precision sifted +/-10% size variation aluminum oxide 1000 for probably $50/pound. The cost goes up exponentially for carefully sifted particles, simple as that. Example: Here is 'Comco C powder' comparing their particle size variation to 'the others' using a bell curve. In this case 55 microns. Note Comco's bell curve is tighter than 'the others'. Comco is making a claim that their particles vary in size less than the others. 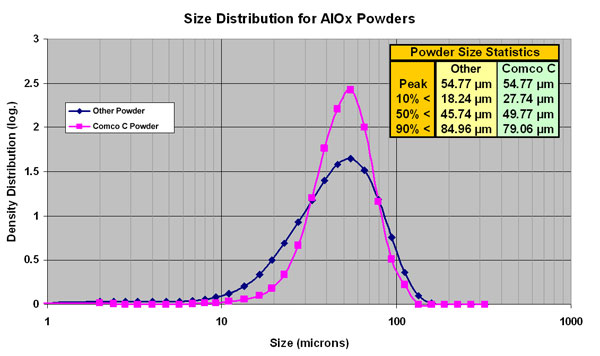 So, let's read what the curve says. Comco claims to have 10% or less particles 79 microns in size. They are basically bragging here because they are saying 'the others' has up to 10% particles 84 microns in size. Either way the variation is big because 79 or 84 microns is way bigger than the advertised 55 microns. Here is the 'grit' to 'micron' conversion chart. 55 microns is close to AO 320. 79 microns is close to AO 250. 84 microns is close to AO 180. So you buy AO 320 and you may get 10% AO 180 ! Smaller particles don't matter so much, but bigger particles sure do. 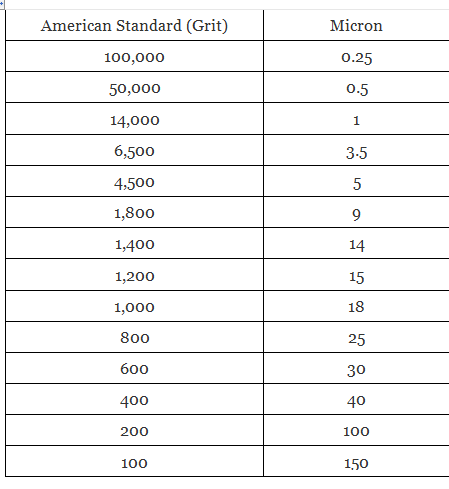 It gets worse for finer grits like AO 500-AO 1000-AO 5000-AO 14,000. As the particle size gets smaller the size variation usually increases because sifting small particles becomes much more of a challenge mechanically. Look at an AO 14,000(1 micron) size distribution chart and you will find much larger variations. Trust there will be 3 micron particles(300% bigger) or AO 6000 in AO 14,000. More accurately 5 micron or AO 4500 in AO 14,000.
|
|
jamesp
Cave Dweller
Member since October 2012
Posts: 36,612
|
Post by jamesp on May 9, 2020 5:45:52 GMT -5
In the tumbling process it does not matter so much if there is a wide size variation in aluminum oxide particles. Our hard Mohs 6 and 7 rocks crush the AO abrasive particles so fast it is a nonissue. We may think we are precision tumbling when we use AO 500 and then AO 1000 but in reality our abrasives are no where near as pure as we think they are. No matter, tumbling has a lot of leeway when it comes to particle size variation because it is so effective at crushing abrasives quickly. Ask Rock Shed or Covington what the size distribution of their aluminum oxide sizes are. Betcha they can't tell you. I must say Rock Shed white AO 500 and AO 14,000 is fine stuff. I have used 3 other brands of AO 500 and could tell no difference. One was grey, two were white and one was brown.
Why would an abrasives application demand super expensive +/-5% AO ? Where high stress metallurgical situations exist like racing engine parts and say helicopter rotor shafts are involved where one slight scratch can cause a fracture propagation. Example would be the inexperienced parts guy that used a diamond scribe to scratch the part numbers on helicopter rotor shafts for Viet Nam Huey's. These scribed rotors kept breaking causing soldiers in action to lose their lives from helicopter crashes.
|
|
jamesp
Cave Dweller
Member since October 2012
Posts: 36,612
|
Post by jamesp on May 9, 2020 5:55:46 GMT -5
El cheapo sand blast grade aluminum oxide particles. 50 pound bag for $40 perhaps: 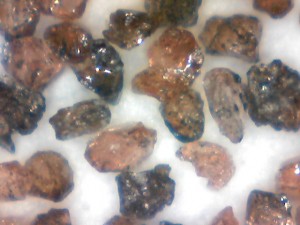 Expensive pre-rounded aluminum oxide particles. This stuff costs way more than $1 per pound. 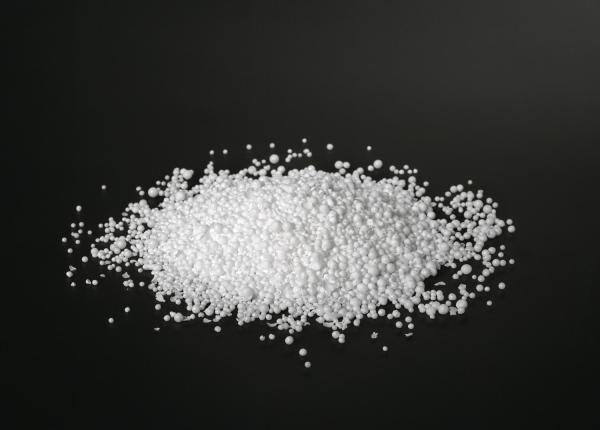 Either will perform near equally in a tumbler. The cheap sand blast grade will look like the pre-rounded after a short while in a tumbler. Actually the cheap stuff is more effective because it cuts for a while before rounding.
|
|
jamesp
Cave Dweller
Member since October 2012
Posts: 36,612
|
Post by jamesp on May 9, 2020 6:06:56 GMT -5
Different aluminum oxide particles under magnification. AO particles particularly made for certain applications. Guessing we use the sharp stuff 99% of the time. But no one knows for sure unless they look at it under a microscope. 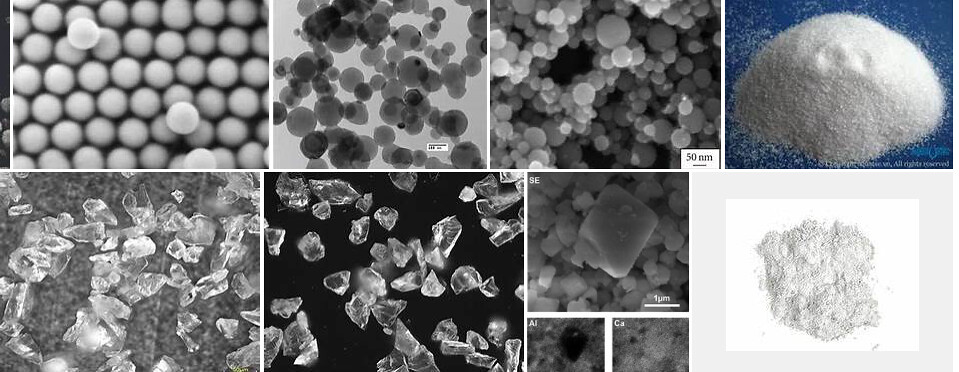
|
|
jamesp
Cave Dweller
Member since October 2012
Posts: 36,612
|
Post by jamesp on May 9, 2020 6:12:29 GMT -5
This is a type of aluminum oxide 14,000(1 micron) powder under 10,000 magnification. Note size variation all over the place. There are AO 100,000, AO 50,000, AO 14,000 and much bigger AO 4000 particles in the mix and is totally legal to market as AO 14,000. 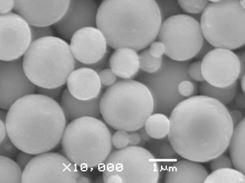 Not a problem. In a tumbler it will polish our rocks just fine.
|
|
|
Post by HankRocks on May 9, 2020 8:07:31 GMT -5
This is a type of aluminum oxide 14,000(1 micron) powder under 10,000 magnification. Note size variation all over the place. There are AO 100,000, AO 50,000, AO 14,000 and much bigger AO 4000 particles in the mix and is totally legal to market as AO 14,000. 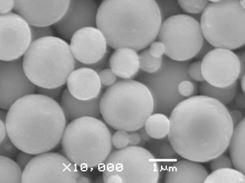 Not a problem. In a tumbler it will polish our rocks just fine. I wonder if the AO in the saved AO slurry I use as a thickener in my AO runs looks as rounded as you pictured here? Whether it does or not, it does make a nice slurry thickener. Really helps with the Ark Quartz, Obsidian and Tiger Eye runs. The wide range of sizes in AO does not surprise me. AO is much more forgiving than say SiC, "smoothing versus cutting". Even there a few grains of coarser grains of SiC grit does not really have much affect on a finer grit run, it get's broken down way too quickly and the finer grit will smooth over and coarser grit scars. I suppose with your super SiC pieces you use leaving one of those in would not be to good as it probably wouldn't break down. That why I only do a soap run between my last SiC run(600) and my first AO run(80 or 500). Henry
|
|
jamesp
Cave Dweller
Member since October 2012
Posts: 36,612
|
Post by jamesp on May 9, 2020 8:23:02 GMT -5
pizzano I bought most of my AO 80 and AO 220 from The Abrasive Armory on Ebay. In this 25 pound bag for this low price. ($36.95 plus $13 shipping) Both are clearly advertised as sand blasting media meaning they are el cheapo grade. I use this AO 220 in the vibe after the rotary is done. It takes the rock to near pre-polish in the vibe using sugar. Next step is AO 14,000 from Rock Shed. So a 2-step vibe finish. This is the EBAY ad for 25 pounds of AO 220: 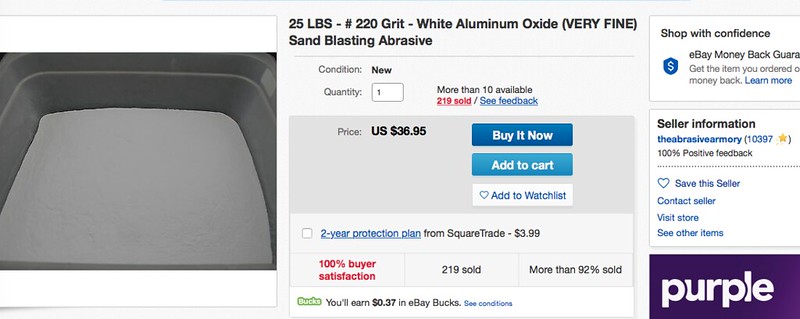 Said AO 220 on glass in vibe this morning after 3 days in sugar. So close to polished the AO 14,000 will have it polished in 4 hours: 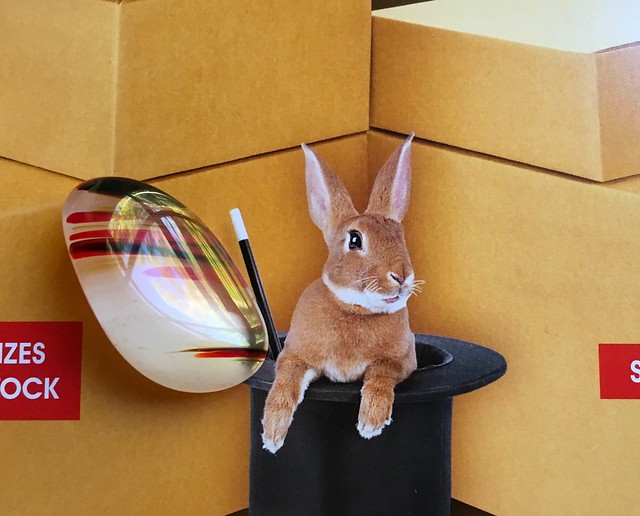
|
|
jamesp
Cave Dweller
Member since October 2012
Posts: 36,612
|
Post by jamesp on May 9, 2020 8:37:07 GMT -5
This is a type of aluminum oxide 14,000(1 micron) powder under 10,000 magnification. Note size variation all over the place. There are AO 100,000, AO 50,000, AO 14,000 and much bigger AO 4000 particles in the mix and is totally legal to market as AO 14,000. 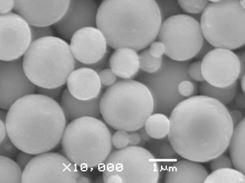 Not a problem. In a tumbler it will polish our rocks just fine. I wonder if the AO in the saved AO slurry I use as a thickener in my AO runs looks as rounded as you pictured here? Whether it does or not, it does make a nice slurry thickener. Really helps with the Ark Quartz, Obsidian and Tiger Eye runs. The wide range of sizes in AO does not surprise me. AO is much more forgiving than say SiC, "smoothing versus cutting". Even there a few grains of coarser grains of SiC grit does not really have much affect on a finer grit run, it get's broken down way too quickly and the finer grit will smooth over and coarser grit scars. I suppose with your super SiC pieces you use leaving one of those in would not be to good as it probably wouldn't break down. That why I only do a soap run between my last SiC run(600) and my first AO run(80 or 500). Henry "That why I only do a soap run between my last SiC run(600) and my first AO run(80 or 500)." If there is ever a time to clean everything absolutely well it would be after the last SiC run Henry. A batch polluted with SiC is a bad thing. Like you said, the AO is so much safer. I can tell you that big AO 22 particles were left over after running a long AO 22 polish run on big rocks in the vibe. I washed and saved these used 1 week old AO 22 particles for close inspection. They were no where near spherical like the above round AO particles. But the sharp edges that make contact with the rocks were rounded. All sharp contact points were rounded. Though they still looked jagged. If you want to destroy a polish toss a few virgin untumbled ceramics in with the batch. They will cut and slash your near polished rocks up in a jiffy. They are made of 98% pure fused aluminum oxide...just bigger particles of AO.
|
|
pizzano
Cave Dweller
Member since February 2018
Posts: 1,390
|
Post by pizzano on May 9, 2020 11:29:59 GMT -5
Jamesp.........That's really good info. I believe you and I had this discussion way back, when I was first experimenting with Vibe tumbling......and you helped alot showing me my errors and common misconceptions.......To this day, I still refer back to our conversations (notes I took) when I'm puzzled. Even did that with this latest batch........I've come a long way since then and have refined my methods to satisfaction since I had found media products that always (predictable) provided very good results, and as you know, I don't tumble glass.
If you remember, I had initially tried a few off-brand compounds like sold at RockTumbler.com and another site (name fails me), and I was routinely (after rough grind rotary) using multiple Vibe stages, AO/CO 120/220, 400, 600, 800, 1000, 1200, 1600 combinations, and constantly complaining about turn-a-round times and clean-up routines..........Then I found Covington's, listened to yours and their advice, applied a few techniques like adding Old Miser (clay) to the 120/220 and 500 stages, and reducing my number of stages and clean-ups in half.
By this time, I had figured out the slurry development and mechanical aspects and had been satisfied (up until now), using an AO or CO 120/220, AO 500, Covington's Tumbler Polish and either Covington's Gold Polish #2 or Cerium Oxide (all purchased at Covington's), on everything I process (Lord knows, I've collected and processed a *hit load of variety) and I'm not afraid or hesitant to try polishing ANYTHING stone related.......lol
Like you've explained and I am somewhat informed, thanks to our previous discussions, there are extreme variations in media product quality. I just have become complacent and spoiled using quality compounds (though even Covington still can't tell me exactly) the micro sizes of their products, just a ballpark figure......lol.
Regardless, I'll not forget this current learning experience..........there's always something new to learn in this hobby. And now, since I've become much more $$$ frugal (out of necessity and not that I haven't been previously with the type of equipment I use.....lol), it shouldn't take me to much time to refine a 3 to 4 step processing method. I've already found a clean-up method that seemed to work with the Rock Shed compounds........better quality stone material then what I currently processed will make a difference.......having known "garbage in-garbage out" from the on-set, it's been a good way to get the "pain" sorted out prior to processing some nicer stuff I have waiting.......!
That's why I posted this thread to begin with.........hoping I'd get some feed-back (thank you Jim), not initially realizing that many here probably haven't much used (or compared) quality like Covington (or other) to the run-of the mill compounds the vast high out-put (more than a few pounds here and there) members tend to process. Though, I'm still not sure that the "you get what you pay for" analogy applies to every case. But it certainly made a difference in my case this time.......!
I'll post some pic's of the results on the previous link I started with this material........so a "soup to nuts" comparison can be made.
Thanks to all who stopped by and glimpsed at my rant.....!
|
|
jamesp
Cave Dweller
Member since October 2012
Posts: 36,612
|
Post by jamesp on May 10, 2020 4:52:15 GMT -5
I inquired about the aluminum oxides that a popular tumbling supply purchases from an abrasives distributor pizzano long ago. The owner had never had such an inquiry. It was a particularly popular aluminum oxide purchased by RTH members. His AO was average quality with quite a wide bell curve(to his surprise). Similar to the blue curve below. 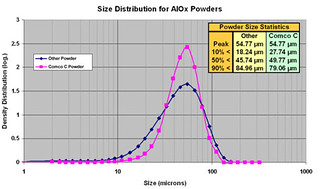 Customers have a right to know the particle size distribution of the abrasives they buy. No different that buying 87-89-91 octane for your car. The abrasive manufacturer uses some fairly sophisticated machinery to crush and separate the crushed particles. Namely a ball mill to crush the raw abrasives and a cyclone separator to separate the particles into different sizes. It is a dirty process requiring a lot of air filtration because they are dealing with blowers moving particle rich air. To attain less variation in particle size the abrasives must be run thru one or more cyclone separation processes therefore increasing costs. Again, for the tumbling process these precision sized abrasives are overkill. A typical abrasives crushing/separating machine: I use a raw silicon carbide that is 3/8" and smaller. It was never run thru the involved cyclone process. It was simply crushed and screened mechanically like road gravel. So it is much cheaper yet adequate for step 1 tumbling (in rugged barrels).
|
|
pizzano
Cave Dweller
Member since February 2018
Posts: 1,390
|
Post by pizzano on May 10, 2020 14:27:50 GMT -5
"Customers have a right to know the particle size distribution of the abrasives they buy.
No different that buying 87-89-91 octane for your car."
It has not been my intent, with this thread, to put a negative spin or praise on any particular compound/media distributor/manufacture. So I hope, those who took the time to review this, found it more informative rather than a knock on Rock Shed or a plug for Covington.........!
Simply thought it would appeal to those who were/are curious about Vibe receipts, by expressing my experience using materials unfamiliar to me and seek some feed back as to experiences other's may have had under similar conditions.......fully realizing that no two Vibe users have the same outcomes, needs, expectations/desires, experience, or process the same material in the same fashion.
As jamesp has so excellently provided, the fact that abrasive manufactures/distributors seldom (if ever) provide any actual verifiable data related to quality, particle, grit size of their products, it seems it can be a "crap shoot" when purchasing various brands as substitutes to what we may have become accustomed to using. Apparently, the quality or grit compound texture of AO or SC is not as critical for rotary rough (60/90 or lower) tumbling stages unless speed and stone volume loss are important to the user, and it can be an issue with certain types of sensitive stone/glass material......particularly after and during the later stages of the process.
As for Vibe application, since most of us Vibe users, do not Vibe (rough grind) raw material with lower than 120/220 grit size, the use of either AO or SC during the (so called) 120/220, 500, 600 stages (depending on stone sensitivity) and additional media (ceramic) applications, come to expect result variations because there can/will be issues due to and related to grit quality and particle size, most often with Alum Oxides. This issue materializes even greater during pre-polish and polishing stage applications, as I discovered.
Since, we currently must live with the lack of quality and factual data related to abrasive compound materials, the only recourse, I guess, is to either pay the price/availability and stick with what we've become accustomed to, or put on another "learning curve" cap, have a few more shots/bottles or draws from the bong, of our favorite numbing agent, and experiment with the run-of-the-mill products readily available......not to mention, at some cost (if one has to try several products) and loss of time associated with reaching a "personal satisfaction" production rate and end quality jewel.........That's my take....and I'm sticking with it.......LOL
Thanks Jim, for your time and wisdom........it is appreciated..!
|
|
Benathema
has rocks in the head
 
God chased me down and made sure I knew He was real June 20, 2022. I've been on a Divine Mission.
Member since November 2019
Posts: 703
|
Post by Benathema on May 10, 2020 14:54:32 GMT -5
This is a good thread. 11/10. I remember a few months ago trying to see if there was a handy conversion factor/formula between grit number and size without much luck. Pretty much have to rely on the tables, but even then, it's more complex. Different countries use different scales, and even within a country there's a multitude of scales. Combine that with say, "what does 100 grit mean?"... It gets messy with what size sifters define the upper and lower bounds of the distribution of particle sizes. Of course, technically it means something and there are metrics, but something like 36, 60, 90, 220 grit is a concept to me at least. With tumbling having so many variables, and almost no two batches are exactly the same, it's bordering on being just a qualitative process, though that doesn't stop us from trying to quantify it!  . To that end, good-enough-for-the-price is the way I go with it, "ehh, close enough"
|
|
jamesp
Cave Dweller
Member since October 2012
Posts: 36,612
|
Post by jamesp on May 11, 2020 4:25:27 GMT -5
Rock tumblers alter abrasive particles due to the hardness of rocks. Look at your rock tumbler as an efficient inexpensive abrasive manufacturing device because it serves as a ball mill to reduce particle size. Many ball mills use EXPENSIVE agate balls(in most cases Brazilian agate) to crush abrasives to specified sizes. Or(ALSO EXPENSIVE) Mohs 8+ aluminum oxide balls, the same aluminum oxide fused ceramic that(most of) our ceramic media is made of. 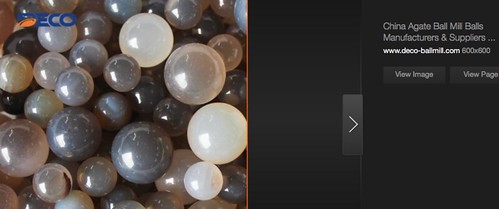 A baby ball mill for lab use. Even the tumbler(ball mill) barrel is made of aluminum oxide. $$$ 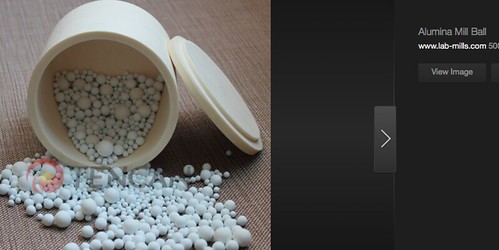 Finishing rocks: A good abrasive analogy is AO or garnet sandpaper used on wood furniture(or most metals). In this case the wood or metal is much softer than Mohs 5-6-7 rocks so the abrasive particles never 'break down' as in a rock tumbler. Instead the sandpaper gets plugged up or the particles fall away from the bonding agent rendering it no longer effective. If 400 grit sandpaper has 100 or 200 grit particles it is likely that the wood will have scratches in it. If the final 1200 sandpaper has 100 to 200 grit particles in it the wood will have even worse relative scratches in it. Where as in a tumbler this issue of larger particles is way less an issue because our tumblers crush/wear/reduce/break down abrasive particles. Not only do Mohs 5-6-7 rocks break down abrasives but they tend to break down larger abrasive particles quicker. This is why aluminum oxide polish can be reused several times, the smaller the AO particle the more structural strength it has. One micron/14,000 grit AO polish particles are more durable than AO 220 or AO 500 particles and can be reused up to a point. No chance of reusing AO 80-220-500 in a rock tumbler for pre-polish steps. Shaping rocks: Silicon carbide is the ultimate shaping/cutting abrasive. Silicon carbide dances to a completely different drummer since it is way more brittle than aluminum oxide in that it has a shorter life in a rock tumbler. It is constantly shattering into approximately half sizes by design creating sharp edges because it was designed for aggressive cutting. Call it binary breakage rates. SiC is also more expensive to compared to AO since most raw white clays are composed of a high percentage AO. Another good reason to use slurry thickeners with SiC to avoid crushing your SiC into oblivion due to rocks slamming into each other and crushing the SiC before it can 'cut' rocks. You get way more mileage out of SiC if your rocks are not slamming and banging against each other by sticking them together with a liquid thicker than straight water. The thicker slurry creates more rubbing action that wears rocks much quicker.
|
|
Prov
starting to spend too much on rocks

Member since March 2020
Posts: 116
|
Post by Prov on May 18, 2020 12:40:05 GMT -5
This has been a really informative thread. These kinds of knowledge dumps are the best!
|
|
|
Post by scienceteacher79 on Nov 28, 2020 21:52:10 GMT -5
An excellent series of comments, posts, and photos. I loved the graphs and explanations. A very informative read. Thanks for taking the time to post. Valuable insights here. It is worth the entire read. Good Job!
|
|