QuailRiver
fully equipped rock polisher
 
Member since May 2008
Posts: 1,640
|
Post by QuailRiver on Aug 15, 2019 18:16:58 GMT -5
I see that the CL author has deleted the listing now so I don't know if you were lucky enough to buy it or not. I have a Fac-ette machine and like it very much. Fac-ette just closed their doors for good at teh end of last year. But my understanding is that the micro meters can still be purchased through the company that manufactured them for Fac-ette. If you need their contact info let me know and I will see if I still have it. A clean moderately used Fac-ette machine with micro meter, and all in good working condition starts at $2K and goes up depending on the accessories included. If you want to get into faceting, IMHO you couldn't find a better machine. If you were able to buy the Fac-ette on CL for a good price and are not looking to get into faceting and just want a flat lap, then you could probably sell the used Fac-ette for enough money to buy any brand new flat lap on the market and still have money left over to buy some cool cutting rough! Quail River I stumbled on this forum while searching for the micrometer. can you give me the name of the manufacturer for the Fac-ette micro meter? Sent you a PM. Larry C.
|
|
QuailRiver
fully equipped rock polisher
 
Member since May 2008
Posts: 1,640
|
Post by QuailRiver on Aug 10, 2019 12:23:58 GMT -5
|
|
QuailRiver
fully equipped rock polisher
 
Member since May 2008
Posts: 1,640
|
Post by QuailRiver on Aug 10, 2019 12:02:42 GMT -5
Hi KD please go to my web site gemsmineralsfossils.com I have few crystal specimens from $30 to $60. If any of them will work for you, just pm me and I will sell it to you direct. Larry Huffman We are pretty careful with allowing members under 100 posts to sell but I can vouch for Larry - he's been on the forum here since 2009. He just had a bit of login trouble and ended up opening a new account. I vouch for Larry Huffman as well. I have meet him and done business with him a couple of times and found him to be a great guy. Larry C.
|
|
QuailRiver
fully equipped rock polisher
 
Member since May 2008
Posts: 1,640
|
Post by QuailRiver on Aug 5, 2019 13:01:09 GMT -5
Update 8/10/2019 - This item is now SOLD. Thank you!  I have a 1970s Ultra Tec V2 faceting machine for sale. This machine has a brand new Ultra Tec factory speed control unit installed, a new rubber splash pan, a new solid walnut base (the new speed control units are taller than the old ones so it required a new taller base), and a new set of German made NTN brand arbor bearings (same make as the originals). This machine is very clean and in good condition, and also comes with a flexible Moffat light, a replacement drip pot, a 64 index gear, and two Allen wrenches. I have cut a Barion Emerald Cut test stone on this machine and though the accuracy is not equal to a new machine, I was still able to cut a commercial grade (or better) stone with it. I did not have to use the cheater at all until after I had cut the pavilion and transferred the stone to another dop and was finishing up the first row of crown facets when the stone came unglued from the dop. I had to re-dop the stone to finish the crown, and so at that point had to use the cheater to realign the second and third rows of crown facets. But in order to show the level of meetpoint accuracy of this machine. I have posted several photos of the test stone's pavilion taken at various angles on my flickr page to show the varying meets which were made without having used the cheater (see link below). These older model V2 machines did not use keyed dops but rather have a removable keyed tapered dop collect in which 1/4" diameter shaft dops are inserted and secured with the collet's set screw. The original UT dops, the dop collet key, and the UT tapered shaft 45 degree table adapter were not with this machine when I acquired it. But it works fine leaving the original tapered collet fixed in place and using any standard 1/4" shaft dops and 1/4" shaft 45 degree table dop. When cutting the test stone with this machine I used standard non-keyed Graves brand dops, a Graves brand 45 degree table dop, and a Graves transfer jig all with no issues. To see additional photos of the machine and test stone at this link - www.flickr.com/photos/quailriver/*NOTE: 8/8 Update - I had also posted this machine on eBay and it has an opening bid now so is on longer available to purchase outside of eBay. If still interested you can view the machine eBay listing at the following link: www.ebay.com/itm/Ultra-Tec-V2-Faceting-Machine/123866662232?hash=item1cd7074558:g:uE4AAOSwlqVdSkQ3Thanks for looking! Larry C.
|
|
QuailRiver
fully equipped rock polisher
 
Member since May 2008
Posts: 1,640
|
Post by QuailRiver on Jul 6, 2019 21:13:00 GMT -5
I've seen silent auctions at rock shows. First silent trade I've heard of. LOL!
|
|
QuailRiver
fully equipped rock polisher
 
Member since May 2008
Posts: 1,640
|
Post by QuailRiver on Jul 6, 2019 0:56:04 GMT -5
Very sad news! Prayers for Sophia and family!
Larry C.
|
|
QuailRiver
fully equipped rock polisher
 
Member since May 2008
Posts: 1,640
|
Post by QuailRiver on Jun 26, 2019 21:19:26 GMT -5
|
|
QuailRiver
fully equipped rock polisher
 
Member since May 2008
Posts: 1,640
|
Post by QuailRiver on Jun 26, 2019 21:11:59 GMT -5
Pro-slicer blades used to be considered good blades. But as gemfeller mentioned they were usually used for trimming faceting rough or slicing opal, turquoise and other valuable materials. I think the last one I had was made in the 1990s and it was a good blade. But they, like the rest of the old name brands may be outsourcing production overseas now.
Larry C.
|
|
QuailRiver
fully equipped rock polisher
 
Member since May 2008
Posts: 1,640
|
Post by QuailRiver on Jun 20, 2019 8:14:10 GMT -5
An antique dealer that I worked for in my youth once gave me what I considered wise advice - "Never love anything that can't love you back".
That said, nice slab rockindad. And nice cab/pendant Tela. And nice photo too. If you don't mind sharing the info Tela, what type of lighting did you use for that photo?
Larry C.
|
|
QuailRiver
fully equipped rock polisher
 
Member since May 2008
Posts: 1,640
|
Post by QuailRiver on Jun 12, 2019 23:15:51 GMT -5
QuailRiverLarry, If you are looking for something more aggressive than your 60# sintered, I highly recommend textured 80# wheels. The 80# removes a lot of material very quickly. Textured wheels are significantly more aggressive than regular sintered wheels. Baltic Abrasives is where I purchase mine. www.baltic-abrasives.com/en/lapidary-wheels/textured-wheels/Roger You may have misread, I don't yet have a 60 grit sintered. Just have 30, 80 & 220 in sintered. I've considered the Crystalite Turbine and Crystalite Diamondback wheels in coarser grits (60 or 100) for rough doming but they are nearly as costly as the Inland sintered wheels (at Johnson Bros prices). I think I have 180 and 260 Crystalite Turbine wheels in 6" diameter around here somewhere but have never mounted or used them for performance comparison to other wheels. Larry C.
|
|
QuailRiver
fully equipped rock polisher
 
Member since May 2008
Posts: 1,640
|
Post by QuailRiver on Jun 11, 2019 13:25:32 GMT -5
... also try to avoid lining up the blade on the rounded side of the rock, this can make your blade veer off course and cause dishing if the rock is sizable just my 2 cents worth i have had a saw for 2 years,and roached 3 blades already! One of the "old timers" tricks I was taught when slabbing into a rounded surface is that once the cutting action begins, let the blade cut about 1/4" deep into the rock and then stop the saw and back the vise carriage and rock back to the original position and then restart the saw. By doing this, if the rounded edge of the rock has started causing the blade to veer off from straight, the blade will not be damaged by continuing to be forced to cut further on a non-straight path. The 1/4" deep notch from the first cut will relieve some of the resistance stress on the blade when restarted. And the rock facing side edge of the blade kerf will grind away a little of the meeting edge of the 1/4" notch in the rock and this will help the blade follow a straighter path once cutting resumes. This trick is not foolproof, and if done often will cause some wear on the outer side edge of the blade kerf. But it does lower the risk of cupping an otherwise good blade. Larry C.
|
|
QuailRiver
fully equipped rock polisher
 
Member since May 2008
Posts: 1,640
|
Post by QuailRiver on Jun 11, 2019 12:55:14 GMT -5
There is no reason a properly clamped rock should "fall out" of the vise. And once a first cut is made the rock should not be removed from the vise and re-clamped until all slabs have been cut that can be cut (unless the material is found to be unworthy of continuing slabbing) and the rock clamp has become too close to the blade to cut further without the blade hitting the vise. If there is still good material left on the rock then at that point the rock will need to be moved over, or repositioned in order to produce more slabs. And if just moving over, sometimes the shape of the rock can be a little difficult to get the slabbed face exactly flush or parallel with the blade again.
As hookedonrocks suggested, get a good assortment of wooden wedges in various sizes and cut at various angles to use to help secure the rocks in position prior to the final tightening of the vise. When using medium to large saws I've also found having several rectangular shaped pieces of 3/16" and 1/4" thick, 2" wide Masonite ranging from 2" to 6" long to be helpful for filling gaps between a rock face and vice. These can be stacked and Masonite is soft enough for the rock surface to bite into. And when the vise is tightened and they are compressed they do no have a tenancy to slip.
Larry C.
|
|
QuailRiver
fully equipped rock polisher
 
Member since May 2008
Posts: 1,640
|
Post by QuailRiver on Jun 10, 2019 23:52:44 GMT -5
@qualriver I have a 46grit hex diamond wheel and I only use it on big stuff and yes it chips like crazy and you have to be real careful. However when you get big pieces like bookends that won't sit up correctly you have to remove that material with something. I have a 10mm thick slab of polychrome jasper I plan to grind down with the wheel but will have to be careful not to chip too much off. I only use on cabs as a last resort. My normal cab wheel is a 60 grit. 80grit was too slow. 46 too fast. Still some chipping but seemed a good compromise to me. Let me know what you decide and how you like it. I am interested if there is something better. I finally got around to purchasing an Inland 30 grit sintered wheel a few weeks ago. Got a really good deal on a new-old-stock one on eBay. And mounted it this past weekend. 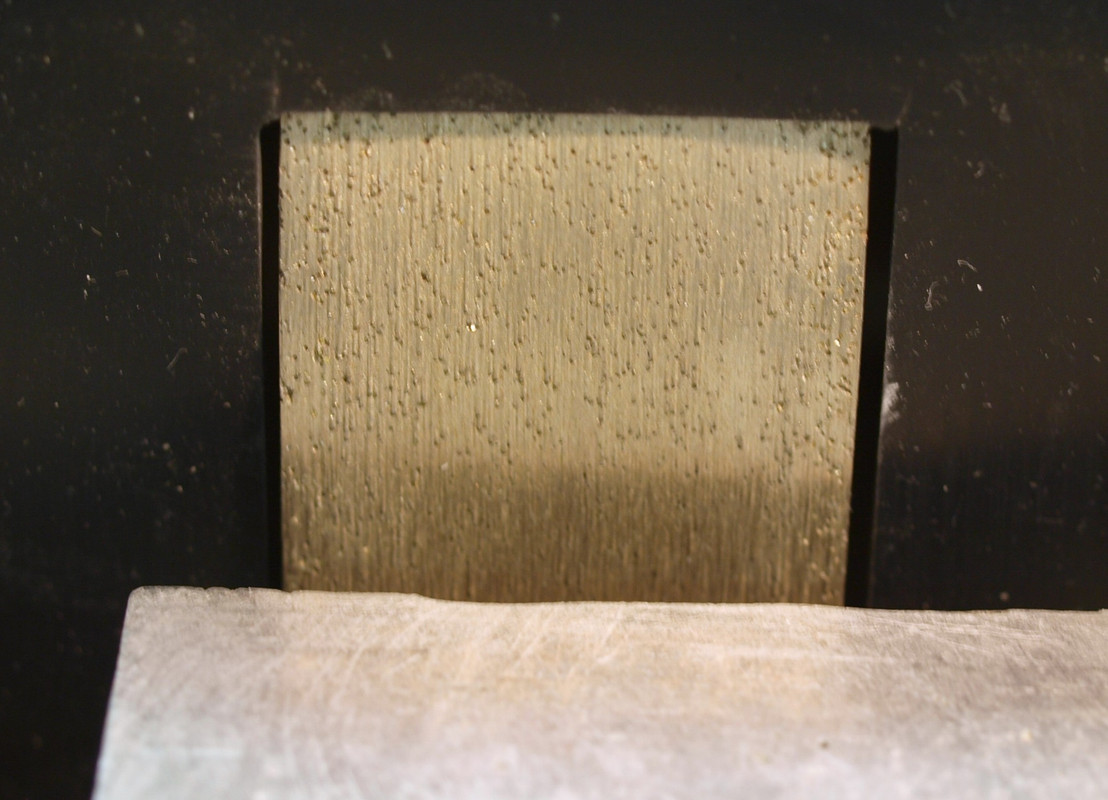 Since adding a new grit wheel was going to require changing the old wheel configuration I figured while I was at it I would add a neoprene splash curtain, which I've been wanting to do for a long time now. It's made from 1/16" thick sheet neoprene rubber and is working better than expected - no more getting soaked while grinding! 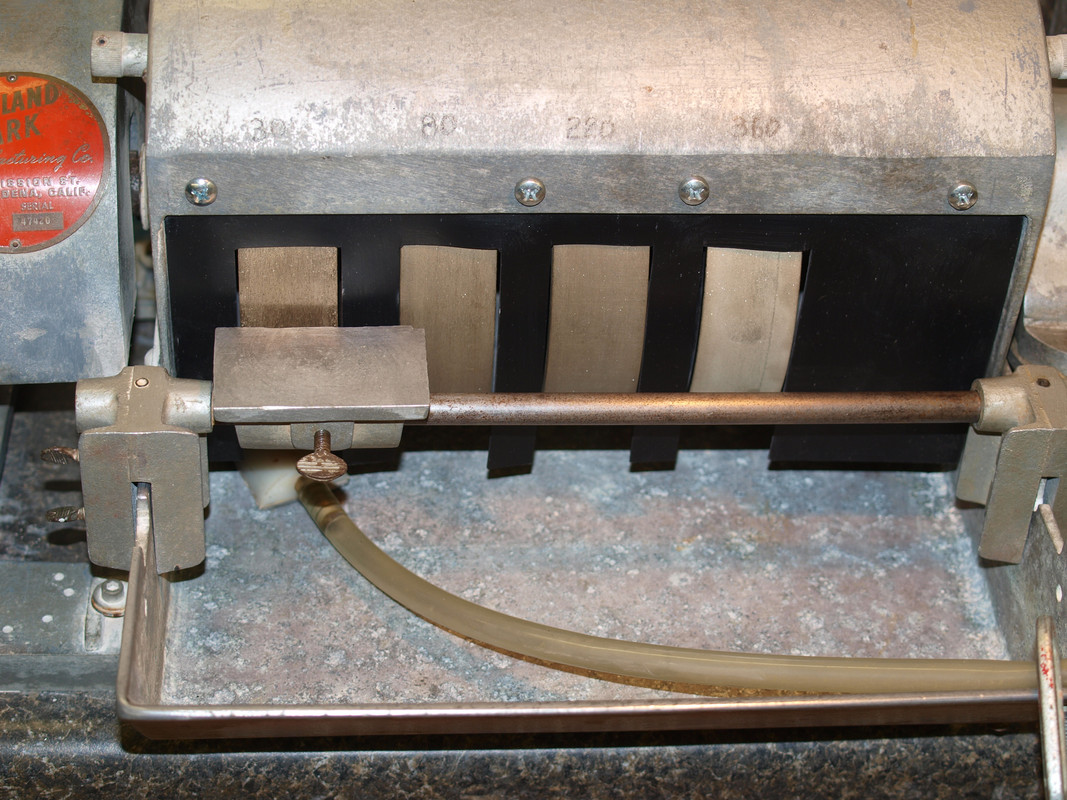 The 30 grit sintered wheel is a little bit "chippy" as I was afraid it may be. You can see the typical chipping on the edges of the marked preforms below. The chipping on the underneath side is a little worse but since those areas get ground away when domeing I didn't bother showing them. In the future I think as long as I stay 1mm to 1.5mm away from the final shape markings that then I can bring in the final shape on the 80 grit sintered and that will remove most of the chipping from the 30 grit. 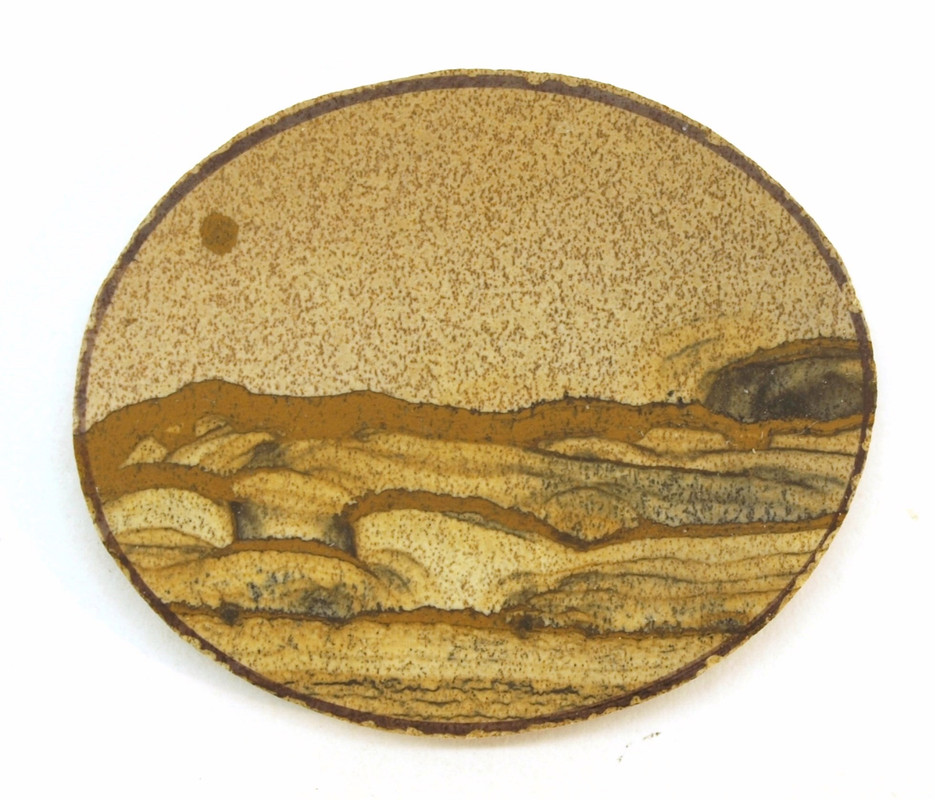 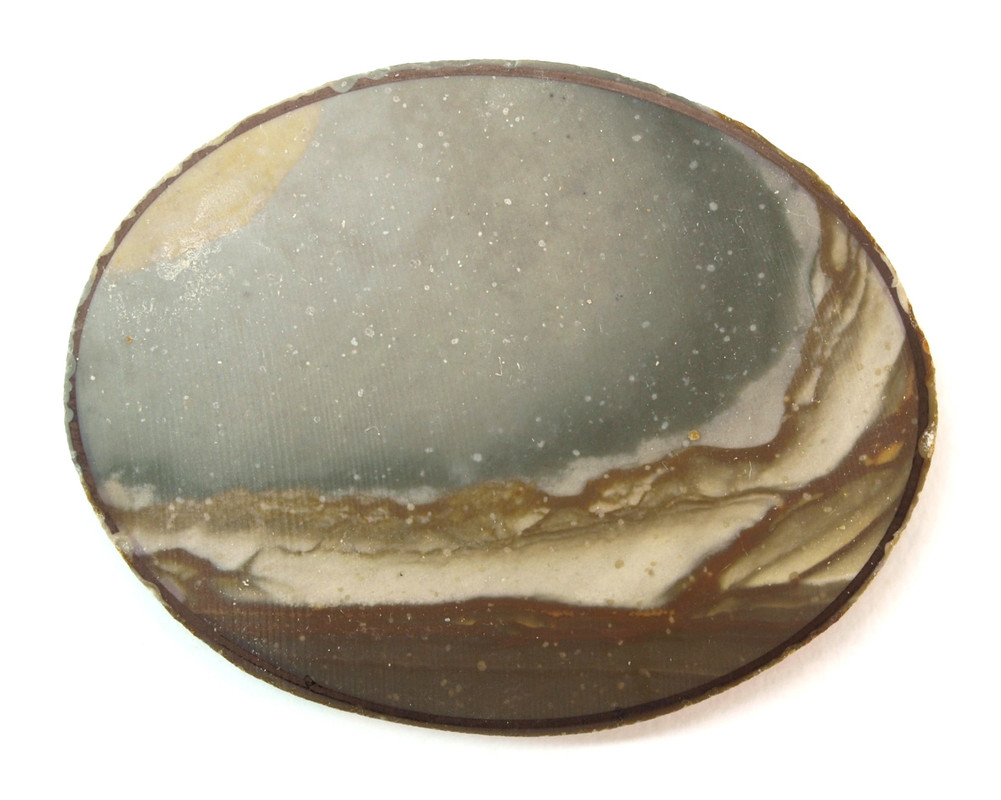 As far as performance goes it's not quite the beast it would appear to be but still cuts about three or four times faster than the 80 grit HANS sintered wheel next to it. It does leave deep scratches so will always have to leave a little more material for the next stage to prevent running into leftover scratches when sanding. I pre-formed fifty cabs with it this afternoon. Mostly larger cabs of jaspers and agates and found performance slowed down significantly after about twenty cabs. But a light dressing with a SC dressing stick brought some spunk back to it. As far as my opinion on if it was worth adding this wheel to the line up, I guess in my case it was because the HANS sintered 80 grit I have cuts slowly (more like a 120 or 150 grit plated wheel) so it is not a time efficient pre-former. I should have originally ordered a 60 grit instead of an 80 grit. The addition of the 30 grit sintered followed by the 80 grit sintered probably takes about the same amount of time as it would just using a 60 grit sintered to pre-form. So if I hadn't gotten a deal on it and had had to pay retail, I probably would have been just as well off (production time wise) to have just ordered a 60 grit Inland sintered to replace the HANS 80 grit sintered. Larry C.
|
|
QuailRiver
fully equipped rock polisher
 
Member since May 2008
Posts: 1,640
|
Post by QuailRiver on Jun 1, 2019 0:30:02 GMT -5
Been meaning to post this for a while now just to give everyone a heads up - Microsoft is discontinuing support for Windows 7 January 14th, 2020. So anyone who may still be using this system (including my wife and I) may want to take this into consideration prior to sinking anymore cash into a windows 7 system. And also may want to upgrade to a more current system prior to then, for security reasons.
Larry C.
|
|
QuailRiver
fully equipped rock polisher
 
Member since May 2008
Posts: 1,640
|
Post by QuailRiver on May 21, 2019 23:36:02 GMT -5
I keep a 360gt Crystalite Crystalring wheel mounted in my line-up just for such occasions. I wish that DP made a 360 or 400 grit Nova.
Larry C.
|
|
QuailRiver
fully equipped rock polisher
 
Member since May 2008
Posts: 1,640
|
Post by QuailRiver on May 21, 2019 11:19:17 GMT -5
Very nice Richardson's Moss! The last one resembles Maury Mountain Moss Agate.
Larry C.
|
|
QuailRiver
fully equipped rock polisher
 
Member since May 2008
Posts: 1,640
|
Post by QuailRiver on May 19, 2019 11:13:57 GMT -5
I have one of those rail slide clamps for a model J but seldom use it. On mine the left side rail isn't quite parallel to the blade so it would be a little rough on the blade if I used it much. But my vise didn't come with the saw, it was a latter acquisition. My Rock Rascal was made in the early 1980s and the clamp, if I remember correctly, I ordered in the late 90s. I can't remember if the optional vise was even available in the early 80s so they may not have been making the saws with a true parallel-to-blade edge at that time.
I used to use mine a lot with water and Raycool which was an additive that Raytech used to make but found that the blades and bearings don't last as long using water & Raycool so mainly just use it with oil unless I'm trimming something porous in which case I still use water & Raycool.
As far as the rough edge goes you could probably sand it smooth with wet/dry SC paper from the auto parts store and then wax the edge rail with paraffin to make it slicker for the clamp to slide on.
Larry C.
|
|
QuailRiver
fully equipped rock polisher
 
Member since May 2008
Posts: 1,640
|
Post by QuailRiver on May 16, 2019 22:54:05 GMT -5
Here is a formula for stabilizing water glass that I had saved as a document file several years ago. I have not tried using this formula myself. And unfortunately I do not remember who the original author was in order to give them credit. My apologies to the original author for not saving that information. " Here is the Waterglass/Emergen-c silication formula. The addition of Emergen-C makes the silication waterproof where straight Waterglass will not hold up to the lapidary processes.
Since most stones are cut in water and will probably be subjected to immersion and water-based cleaners, waterglass isn't a satisfactory stabilizer. Various chemical processes can cause silicates to polymerize into opal or agate, as occurs in petrified wood. The hardened silicate from my procedure is clear and colorless. It's not as fast as epoxy, but treated material is "rock-solid" --- no undercutting or discoloration with age. In the end, it's also safer, cleaner and a lot cheaper than Opticon or other epoxies.
Here's the general procedure that seems to be working now. It's not as involved as it may seem at first glance, and gets easier with practice.
1) Clean slabs (or rough less than 1" thick) in a solution of hot water and trisodium phosphate (available in most paint departments for wall cleaning) prepared in the concentration specified for grease removal. I let them soak overnight. This may cause some slight color change - deeper blues and greens on chrysocolla and turquoise. Rinse slabs thoroughly and allow to air-dry.
2) For this step, you need a shallow, lidded stainless steel (not iron or aluminum) pot or pan and a means of holding temperature at around 180 F, substantially below boiling. I found a thrift store electric buffet warming plate which worked nicely. The stabilizing formula is based on sodium silicate solution with a weight ratio of around 3.2 (available at <http://www.chemistrystore.com/sodium_silicate.htm> www.chemistrystore.com/sodium_silicate.htm and other similar sources). Read the MSDS! This solution is caustic, and you should wear eye and skin protection to handle it. Spray the pot lid edge with PAM or other cooking spray to keep it from adhering to the pot. Clean up drips and used utensils immediately with warm water. If the solution gets on fabric, rinse and wash it before the silicate dries.
3) Now, this is where things get a little weird... it takes a combination of very low activity organic acid and alkali mineral salts (carbonates, phosphates and sulfates of calcium, potassium, etc.) to get the silicate to polymerize in a non-water-soluble form, e.g. as agate. Though this can be done with very concentrated mineral water (about 1 gallon boiled down to 1 cup) and aspirin or citric acid, I found the easiest and cheapest way to do this was with Emer-Gen-C Lite mineral supplement packets. ***It's important to get the Lite sugar-free version --- sugar or fructose will oxidize and may discolor the stones.*** Dissolve one packet of Emer-gen-C in 1 cup (approx. 250 ml) of water and allow the fizzing to disperse. Add this solution to 8 oz. of sodium silicate in the stainless steel pot and stir to mix. For stones with very fine porosities or hairline cracks, add about 1 teaspoon of liquid dish soap to reduce the viscosity of the solution.
4) Submerge the slabs in silicate solution in a single layer. Stacked slabs may stick together. Cover and let stand on the heat source for at least 24 hours. Longer cooking won't hurt... I've left some material in for up to 4 days. [For very thick material, a pressure cooker has been suggested, but the risks of silicate splash clogging the vent mechanism are too great for my peace of mind.]
Remove the slabs and set them on a spray-greased baking rack over newspaper. Allow the slabs to drip dry. The dried slabs are safe to handle bare-handed, and can be gently pried off the rack if they stick. A word of caution --- dried silicate can be as sharp as glass!
5) Place the dry slabs on a cookie sheet and set in a cold oven. Turn the oven to "warm" and leave it on overnight. Turn the oven off and allow the stones to cool to room temperature with the door closed. The slabs should look shiny and any deep cracks will be partially filled. Porous stones should feel noticeably heavier after this treatment. at this point, you can re-clean the stone and "paint" silicate formula to fill larger cracks and voids. Repeat the drying and baking processes to set the added silicate.
The whole cleaning, soaking, drying and baking process can be repeated as many times as you feel necessary. There may be some brownish surface discoloration on the stone, but this comes off with polishing.
Silicate solution can be reused multiple times, adding a little water to replenish the volume. The solution may have some precipitated white silica gel and will turn tea-colored. When a thick layer of silica gel has precipitated and the solution seems thin, treat it by pouring out on about a pound of scoopable cat litter, allowing the litter to dry, then discarding it in regular trash. Don't pour it down the sink.
I've tried to explain in as much detail as I've gleaned from a half dozen or so different trials. So far, it's worked on slabs and rough of many different jaspers, chrysocolla, turquoise, Laguna, Botswana, plume and moss agates, Koroit opal, petrified woods and fossil coral." Larry C.
|
|
QuailRiver
fully equipped rock polisher
 
Member since May 2008
Posts: 1,640
|
Post by QuailRiver on May 16, 2019 17:39:49 GMT -5
As far as currently produced diamond blades, the MK/BD-301 is my first choice for slabbing with oil. Although that may be changing soon. I've been using the MK-225 Hot Dog blade that Peruano mentioned for trimming slabs on a Raytech 10" trim/slab saw with Duroprime 90 mineral oil for a coolant and LOVE it! As of today I've trimmed over 560 cab preforms total on this one blade, of mostly agate and jasper with a high percentage being large preforms and preforms cut from large slabs. I've abused the heck out of this blade and it's still got a lot of diamond showing. I haven't tried slabbing with it yet but will probably get a new one now to try for slabbing. If it proves to be as good at slabbing as it is at trimming then it will probably become my go-to blade for 10" and 12" saws. A MK/BD factory technician told me over the phone that the MK-225 Hot Dog blade is the exact same blade as the BD-305 Agate Kutter blade. The Hot Dog blade is a popular 10" tile saw blade for contractors so it can be bought at a much better price from some of the discount industrial supply stores. The 12" version is much more expensive but I plan on getting one of those too to try with water on my vintage 12" Slik Drop Saw this summer. It should be noted that the MK-225 is a little "chippy" and throws micro-gravel like crazy when hand feeding it slabs, especially when new. So if you're going to use one for trimming or slabbing with an open saw DEFINITELY WEAR SAFETY GLASSES!  Larry C.
|
|
QuailRiver
fully equipped rock polisher
 
Member since May 2008
Posts: 1,640
|
Post by QuailRiver on May 11, 2019 23:04:21 GMT -5
Looks like it could be some type of Oolitic agate. Not a true Oolite but one that falls under the generic term as far as the trade/hobby is concerned. True Ooilite formed from ooids have orbs 2mm or less in diameter. I've also seen similar materials referred to as Fish Egg Agate.
Larry C
|
|