QuailRiver
fully equipped rock polisher
 
Member since May 2008
Posts: 1,640
|
Post by QuailRiver on Aug 31, 2022 13:33:57 GMT -5
|
|
QuailRiver
fully equipped rock polisher
 
Member since May 2008
Posts: 1,640
|
Post by QuailRiver on Aug 30, 2022 21:48:27 GMT -5
Don't know of any rock collecting sites in the Wheeling area but there used to be a few large art glass factories there so with a little research you might be able to score some vintage colored slag glass from the dumps from their end-of-the-day pours.
|
|
QuailRiver
fully equipped rock polisher
 
Member since May 2008
Posts: 1,640
|
Post by QuailRiver on Aug 28, 2022 10:59:20 GMT -5
I like the hood design on that Slik 14" on eBay. I don't know if that was stock or not but it looks like it would be fairly easy to replicate for most any model of boxed-in based drop saw.
|
|
QuailRiver
fully equipped rock polisher
 
Member since May 2008
Posts: 1,640
|
Post by QuailRiver on Aug 28, 2022 10:50:20 GMT -5
I have the 12 " version of the Slik Drop Saw that I only use for materials that are best slabbed with water. It can be used with oil too but is very messy. So I only use it outdoors and with water. 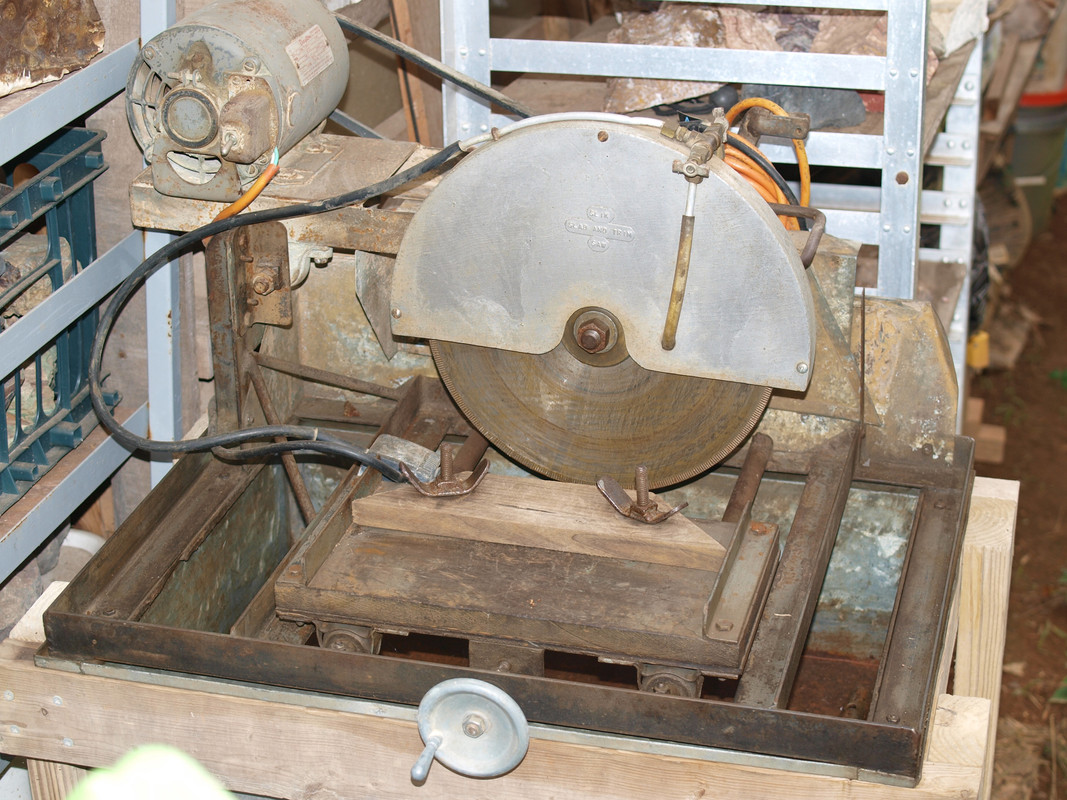 After looking at the rest of the photos of the 14" model linked on eBay I see it is one of the models with the hydraulic mechanism to control the drop of the blade. My 12" model does not.
|
|
QuailRiver
fully equipped rock polisher
 
Member since May 2008
Posts: 1,640
|
Post by QuailRiver on Aug 22, 2022 12:29:53 GMT -5
IMHO the best tool for pre-shaping/prepping rocks for tumbling would be the Rock Rascal model "T" outfitted with a coarse grit diamond wheel (60 or 8o grit). 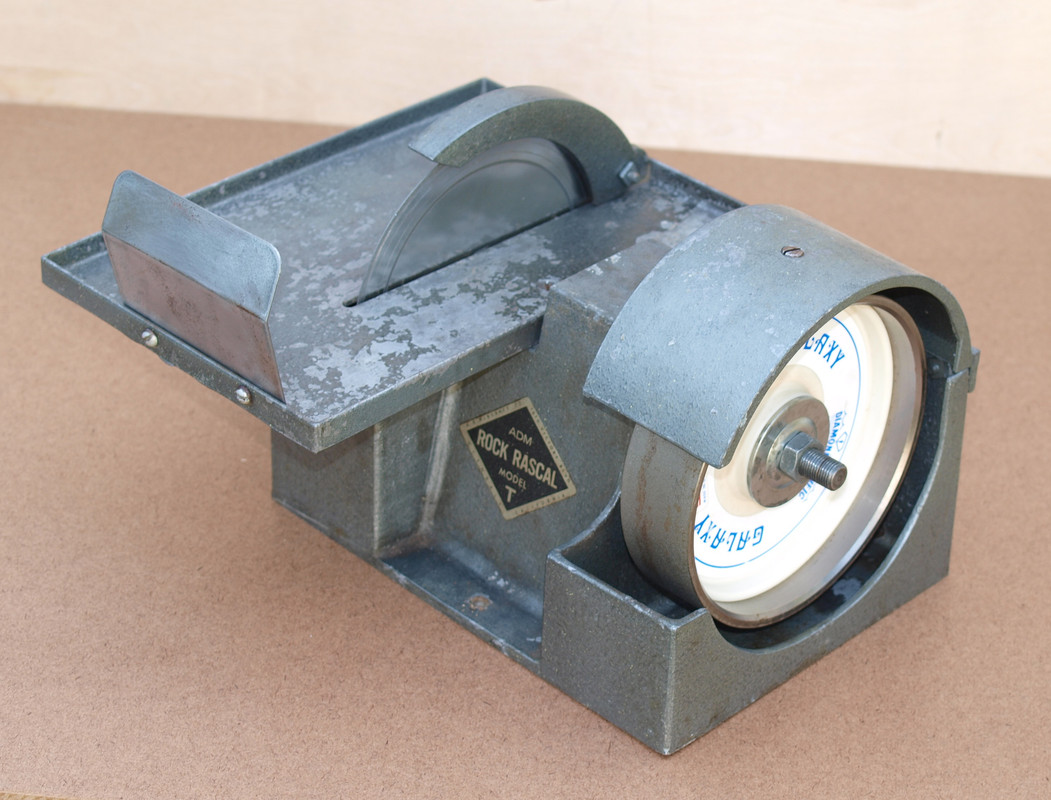
|
|
QuailRiver
fully equipped rock polisher
 
Member since May 2008
Posts: 1,640
|
Post by QuailRiver on Aug 19, 2022 11:29:32 GMT -5
So my question is has Mk's quality dropped in general & would a new MK-303 also not be as good as the older ones? Or is this just showing up on the 225 Hot dog ? Patty Sorry but I haven't purchased a new MK/BD 303 or 301 for several years now so can't answer that question. Perhaps someone else on this board has and will be able to respond? For my medium to larger sized slab saws I usually seek out the old stock U.S. made blades and purchase those when I can find them.(i.e. Vanguard, Felker, Star Diamond, Lortone Black Panther, Congo, the earlier Mk 301 and 297 blades, and the U.S. made Raytech Black Blazer are all good blades.) A few years ago I had a large lot of agate and jasper slab trimming to do and had seen positive comments posted about the MK-225 Hot Dog blades being a good aggressive blade so decided make to give one of the 10" Mk-225 blades a try. It performed very well for trimming slabs and since they were inexpensive I had decided to order a couple more while they are still obtainable. Wish I had done so sooner while they were still better quality.
|
|
QuailRiver
fully equipped rock polisher
 
Member since May 2008
Posts: 1,640
|
Post by QuailRiver on Aug 18, 2022 21:48:45 GMT -5
Great write up on the Raytech unit there, Quailriver! I would be interested to know if this Raytech 10" water/oil saw (equipped with proper Agate Kutter or equivalent), will make SHORT WORK of trimming down the stock (sometimes 2" - 3" in size) that I am going to throw in the tumbler?? I guess that would mean getting soaked with water, very likely though too. Hmm. Just looking to hand feed smaller materials at this time, preform cabs later. [Edit] Found an RTH forum thread that helps describe Raytech L-10S here: forum.rocktumblinghobby.com/thread/42482I haven't used the blade labeled the BD-305 Agate Cutter. But I have used the MK-225 Hot Dog blade which according to the factory tech I talked to before purchasing is the exact same blade as the Agate Kutter blade but just repackaged and marketed for lapidary work. The MK-225 Hot Dog blade is my new favorite trim saw blade! After talking to the factory tech on the phone last summer I bought one of 10" MK-225 blades late in the summer and so far have only used it with oil for trimming slabs on my Raytech 10" saw. And man does it eat through those agate and jasper slabs like no other blade I've ever used. I've been planning to do a review of this blade after trying it for slabbing later when I got around to testing it more. But so far I've trimmed over 350 preforms from slabs, many from larger slabs requiring a lot of cutting and the blade has held up great! The only draw-back I've seen with it so far is that being a slotted blade it's "chippy". Definitely have to wear eye protection when using it without a saw hood. My safety glasses, arms, dust mask and front of my shirt got covered with micro-chips of stone every time I used it. Especially until the blade began getting broken in better. I suspect it will be a great blade for slabbing too but only while using the vice. I wouldn't try free-hand slabbing with a slotted blade because if you let the rock get twisted in your hands and one of the corners of the blade kerf at the cooling slots gets caught on the edge of the rock cut I would imagine that things could get ugly (and potentially dangerous) quickly! As for using the MK-225/BD-305 blade with water I haven't tried that yet and even though they are marketed as being made to be used with water. I could not get the factory tech I spoke with to confirm that they will hold up better than a MK/BD-301 Gemking blade when using water. I tried several times to get an opinion about using water with the MK-225/BD-305 blades and he dodged the question each time. So I would still assume that it's doable slabbing small agates and jaspers using just water but that blade life won't be as good as with using oil. tinyurl.com/yyuy5nw5Larry C. After having recommended the MK-225 Hot Dog Blade on this thread three years ago I feel I should let anyone researching 10" blades know that I am no longer as enthusiastic. Today I received two new MK-225 Hot Dog blades (ordered through Home Depot but the order was drop shipped from MK Diamond Products in Torrance, CA). The quality of these blades appear to have dropped from what they were 3+ years ago. Both blades I received today are cupped. They appear to have gotten cupped during the arbor hole boring/stamping/? process. And both have very little kerf and what kerf they do have feels uneven. They will probably still be okay for trimming slabs but being cupped may be an issue if trying to slab. I may be able to flatten them a little by laying them on the milled flat iron surface of my table saw and tapping them with a wooden block and hammer. Using this method I've been able to straighten older softer steel lapidary blades that have gotten cupped. Not sure if it will work on the MK-225 steel core or not. My older MK-225 blade still has some use left in it so it will probably be a while before I try using these new ones. When I do, if there is a noticeable difference in how they perform when trimming slabs then I will do a follow up post.
|
|
QuailRiver
fully equipped rock polisher
 
Member since May 2008
Posts: 1,640
|
Post by QuailRiver on Aug 18, 2022 21:46:03 GMT -5
After having recommended the MK-225 Hot Dog Blade on this thread three years ago I feel I should let anyone researching 10" blades know that I am no longer as enthusiastic. Today I received two new MK-225 Hot Dog blades (ordered through Home Depot but the order was drop shipped from MK Diamond Products in Torrance, CA). The quality of these blades appear to have dropped from what they were 3+ years ago. Both blades I received today are cupped. They appear to have gotten cupped during the arbor hole boring/stamping/? process. And both have very little kerf and what kerf they do have feels uneven.
They will probably still be okay for trimming slabs but being cupped may be an issue if trying to slab. I may be able to flatten them a little by laying them on the milled flat iron surface of my table saw and tapping them with a wooden block and hammer. Using this method I've been able to straighten older softer steel lapidary blades that have gotten cupped. Not sure if it will work on the MK-225 steel core or not.
My older MK-225 blade still has some use left in it so it will probably be a while before I try using these new ones. When I do, if there is a noticeable difference in how they perform when trimming slabs then I will do a follow up post.
|
|
QuailRiver
fully equipped rock polisher
 
Member since May 2008
Posts: 1,640
|
Post by QuailRiver on Aug 14, 2022 18:12:09 GMT -5
Have you checked to make sure that your wheels are balanced. Out of balanced wheels or a slightly misaligned arbor can cause enough vibration to contribute to cabs breaking along natural fractures or falling off the dop.
That said Larsonite is often not very solid material and is notorious for falling apart when slabbing and cabbing.
|
|
QuailRiver
fully equipped rock polisher
 
Member since May 2008
Posts: 1,640
|
Post by QuailRiver on Aug 13, 2022 0:24:27 GMT -5
The main problem with sanding and pre-polishing a large flat surface on a flat lap is that it can take a LOT of time. With a flat lap on a flat surface the cutting action is most effective nearer the outer parameters of the surface being worked while the fine scratches from the previous grit nearer the center are less affected and remain more persistently. The material being removed can quickly clog up or hinder the cutting action of finer grits (especially on plated flat laps).
When using a drum sander with the finer grits you can sand out scratches across the whole surface of rock more quickly. The finer grits (400 and finer) on a sanding drum are not so aggressive that they would too quickly cut dips or leave grooves onto a flat surface. You just have to be sure to keep the rock moving at all times to prevent that.
Most cabochon backs and smaller faced specimens can be sanded on a standard lapidary expando drum. But for bookends and large polished face specimens, in addition to reciprocating flat laps, and large iron rotary laps with SC grit, many lapidary folks who cut and polish bookends or large face polished specimens use a Bull Wheel sander/polisher with 12" diameter rubber padded drum/s and a convex polishing disc. Others use a Richardson's high speed overhead sander (dry) which has a flexible rubber disc for sanding with SC pads, and a Richardson's Buffer which has a large convex disc with sponge rubber padding and a suede covered polishing surface for polishing with oxides. I think these latter mentioned machines give faster results and are still manufactured by Covington, Highland Park, and Richardson's Rock Ranch. And others were formerly manufactured by Polaris Tool & Machine (formerly known as Rock's and prior to that Texas Rock's).
Hope this helped. I would suggest just doing a little more research. There are videos on Youtube showing how to use reciprocating (vibratory) laps, lapidary flat laps (iron rotary type), Bull Wheels and the Richardson Rock Ranch equipment.
|
|
QuailRiver
fully equipped rock polisher
 
Member since May 2008
Posts: 1,640
|
Post by QuailRiver on Aug 12, 2022 17:30:41 GMT -5
I only slab, cab and facet so don't have any experience polishing large bookend surfaces. I had a couple of dot discs many years ago. It's been so long that I don't remember much about using them other than I only liked them for rough grinding but as best as I remember they wore out pretty fast compared to standard laps.
As for your stated purposes of doing the backs of cabs I think that they are fine for that. And probably would work well for smaller faced specimen surfaces too. But for bookend size flat surfaces I'm not so sure. I would think that using flat lap discs of any kind for the sanding and pre-polishing size grits on bookend sized surfaces would be very time consuming and tedious. Plus could get expensive when using dot discs. I would be inclined to find another method of processing those larger flat surfaces.
That said I know I still didn't answer your question about grit successions. Back in the early to mid 1970s when man made industrial diamonds were still under patent and expensive, the coarser grits were really costly. So when cabbing using diamond instead of SC, many of us started off preforming and shaping with a less expensive 180 grit as our coarse wheel followed by a 360 grit for final shaping before sanding. Then from the 360 plated wheel to 600 sanding belt or resin disc. Then to 1200 pre-polish and depending on the material may next go to a 3000 pre-polish. Then to an oxide polish or if only using diamond then 8k to 14k to 50k polish. Today many people start out with 80 grit plated wheels and then go to a 220 grit wheel before going to sanding.
Faceting small faces follows a different succession. It used to be common that cutters would rough out the stone with a 260 grit plated lap and then jump to a 1200 plated lap for most materials. Some materials like corundum would undercut on 1200 so the next step after 260 would be reduced to 600. Then 3K on a copper or tin lap for a pre-polish. But nowadays many faceters don't want to risk sub surface damage to their material so the coarsest grit they will use for roughing is 360. Then on to 600 or 1200 or depending on the material may even skip the 1200 and go to 3k or 8k pre-polish. I know that all of this doesn't directly address your situation but I included it to illustrate how broad the gaps can be depending on materials and applications. And how narrow for others.
To reiterate, I think the dot disc will work fine for you for doing the backs of cabs and smaller polished faced specimens. But I have real doubts about them working well on larger surfaces - especially in the mid range to fine grits. For the former, choosing three of the given grit options you state are available to you, I would be inclined to try [60] 120-325-600 then to diamond belts on expando drums for anything finer. And if you find the 120-325 to be too large of a jump then you can always add a 220 into the line-up later.
|
|
QuailRiver
fully equipped rock polisher
 
Member since May 2008
Posts: 1,640
|
Post by QuailRiver on Aug 11, 2022 14:57:49 GMT -5
What do you plan to use them for - cabbing, faceting, flat lapping?
|
|
QuailRiver
fully equipped rock polisher
 
Member since May 2008
Posts: 1,640
|
Post by QuailRiver on Aug 8, 2022 17:47:16 GMT -5
Many years ago I saw a unit with the same type double end arbor that had burned out. And the owner had removed all of the winding and electrical guts from the motor and cut a large square hole in the back of the motor. He added a pulley to the center of the arbor shaft and ran a v-belt though the square hole he had cut in the back of the motor housing to a 1/3hp continuous duty/general purpose motor so that he could continue to use his cabbing unit without having to replace the more expensive double ended arbor motor. He essentially turned his double ended arbor motor into a functioning arbor similar to the Lortone ProMax unit except the belt and motor were to the rear rather than on top. 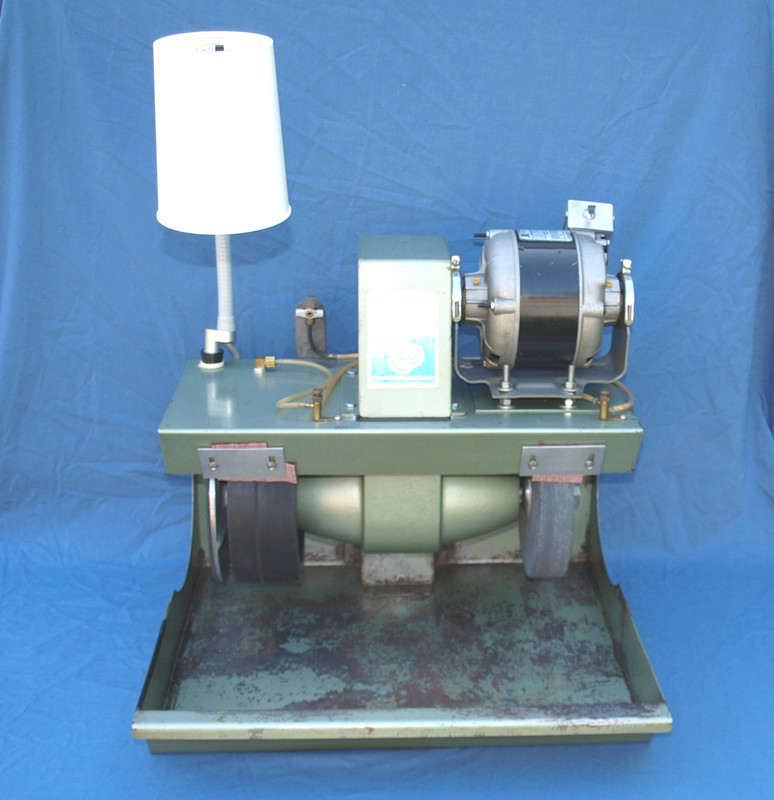
|
|
QuailRiver
fully equipped rock polisher
 
Member since May 2008
Posts: 1,640
|
Post by QuailRiver on Aug 8, 2022 17:24:37 GMT -5
Right after posting that last post I noticed where you are from. I don't know about nowadays but back in the 1970s Johnson City, TN used to have a large club with lots of members. They also used to have a fairly good sized indoor show. So if the club is still around, and since you aren't too far away, you may be able to get in touch with someone thru the club that has a slab saw and is in the area who you can work out a deal with to slab your Larsonite.
|
|
QuailRiver
fully equipped rock polisher
 
Member since May 2008
Posts: 1,640
|
Post by QuailRiver on Aug 8, 2022 17:17:05 GMT -5
Larsonite can have a habit of separating at seams. So I wouldn't try any drilling or "controlled breaking" techniques unless you don't mind turning a portion of it into tumbling rough. Over the course of time as I found myself with a nice piece of rough too large for my saws at any given time, If I couldn't find someone to slice it for me for a reasonable trade then I usually just hung onto it until I did have a saw large enough. Started out with a 6" saw 50 years ago and keep adding. Am up to 20" now but still have a few pieces too large for the 20" so am letting them sit and wait. (One of them a large piece of petrified palm has been waiting since 1980.) Good rough is too hard to come by to risk destroying and very little of it is worth damaging a saw/saw blade for, especially on larger saws.
|
|
QuailRiver
fully equipped rock polisher
 
Member since May 2008
Posts: 1,640
|
Post by QuailRiver on Aug 7, 2022 18:09:27 GMT -5
I recently acquired these three Chicken Track Picture Rock slabs from a dealer. It had been a very long time since I had seen any of this grade of this material for sale. They were a little on the pricey side but were just too darn enchanting to pass up. 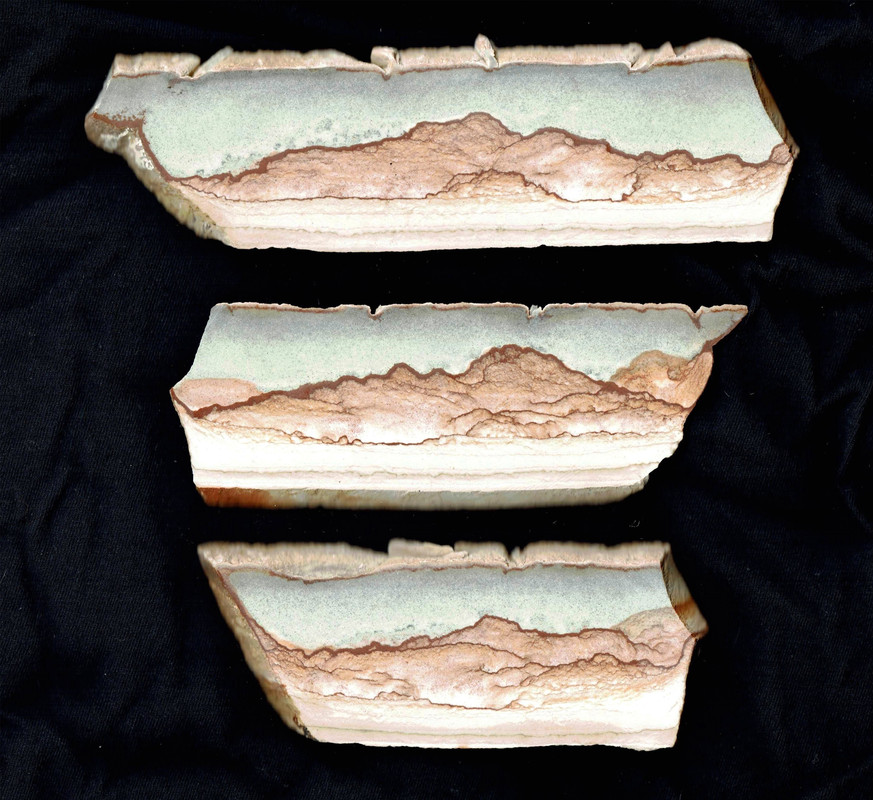
|
|
|
|
QuailRiver
fully equipped rock polisher
 
Member since May 2008
Posts: 1,640
|
Post by QuailRiver on Jul 3, 2022 18:36:16 GMT -5
They've dropped the price down to $850. The craftsman B&I GemMaker unit and the saw are going to need a little elbow grease and probably minor work but IMO the lowered price is fair. A 12" saw for slabbing and trimming, the old Crown cabbing unit for cab shaping and sanding, and after removing the faceting head the old B&I GemMaker units are great for polishing with oxides on flat discs with felt, suede, or canvas. So as Hummingbird stated, this would be an okay starter package for someone wanting to get into lapidary on the cheap.
The B&I faceting heads are a 1940s hobby oriented design and only came with a 32 index so are limited to very simple cutting designs. Their arbors have step pulleys for changing speeds. So if one has the patience of Jobe they can buy the laps needed and facet with it too!
The B&I faceting heads still turn up from time to time but the dop stick sets for them are very difficult to find. Also the B&I faceting heads had paper and/or foil printed indexes on the protractor and faceting gear which are usually in poor shape but with a little help from CAD software can be replaced with new PC printed ones.
|
|
QuailRiver
fully equipped rock polisher
 
Member since May 2008
Posts: 1,640
|
Post by QuailRiver on Apr 23, 2022 20:44:19 GMT -5
I switched from SC belts to resin belts and resin pads with diamond paste around 1977 and used them until the early 2000's. Instead of using extender fluid with the diamond paste I used spray silicon as advised by the dealer who sold me the equipment (careful not to breathe any overspray). In the early 2000s I began having trouble finding resin belts that would stay glued at the seam. I had several come unglued after barely being used so I switched over to using 3M diamond cloth belts. The first couple of sets of those I had were really good but they started out-sourcing production and the quality went to them being a big waste of money. With the outsourced belts I would be lucky to get more than two or three large agate cabs sanded before they were nearly worn out. So at that point I switched over to Diamond Pacific's Nova wheels which I still use.
The only draw backs of the diamond paste on resin belts and pads were; the having to use a man made lubricant, and having to be careful to make sure to thoroughly clean the cab between sanding stages to make sure to get any diamond paste residue off. I used cigarette lighter fluid (NAPTHA) to clean off the diamond paste residue. Other than that the paste on resin belts/pads worked fine.
|
|